MKII_Supra
Member
The engine was fitted today to check clearances for radiator, fans, manifolds, exhaust, hood clearance, and turbo placement. Using PeeWee's mounts (purchased pre-built from Nick), I mounted the engine with the mounts allowing for the most front clearance. (I.E., mounts farthest forward on engine block)
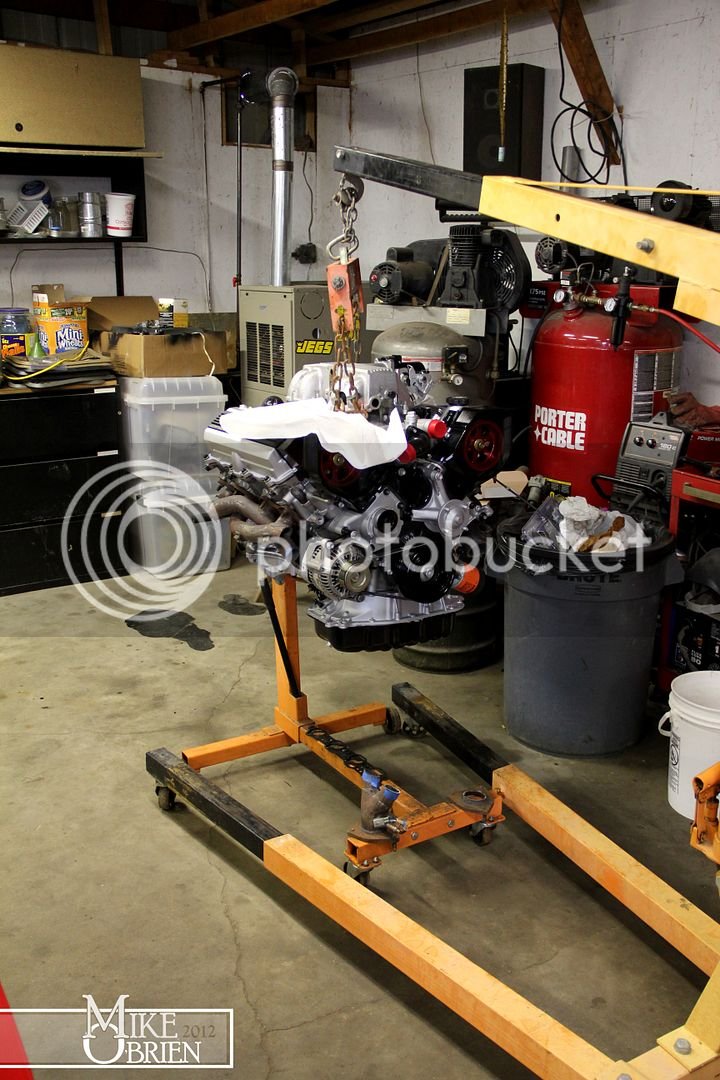
I had to dig around for my old set of lower mounts, and found it easiest to mount the lowers to the uppers after seeing that one of the passenger manifold's (flipped driver's manifold) primaries was contacting the lower mount and preventing them from mating.
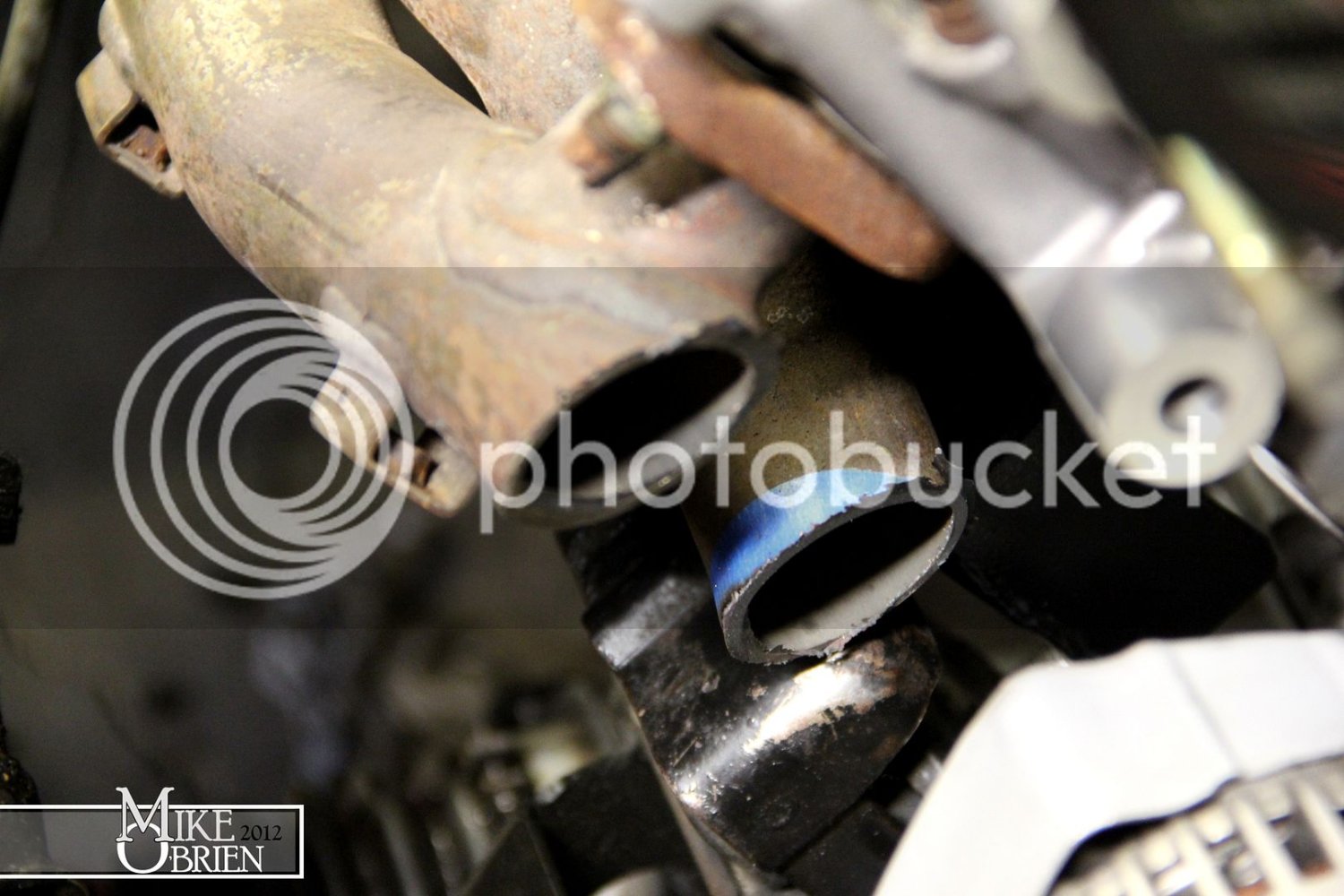
I removed the passenger manifold, and set the engine on its perches.
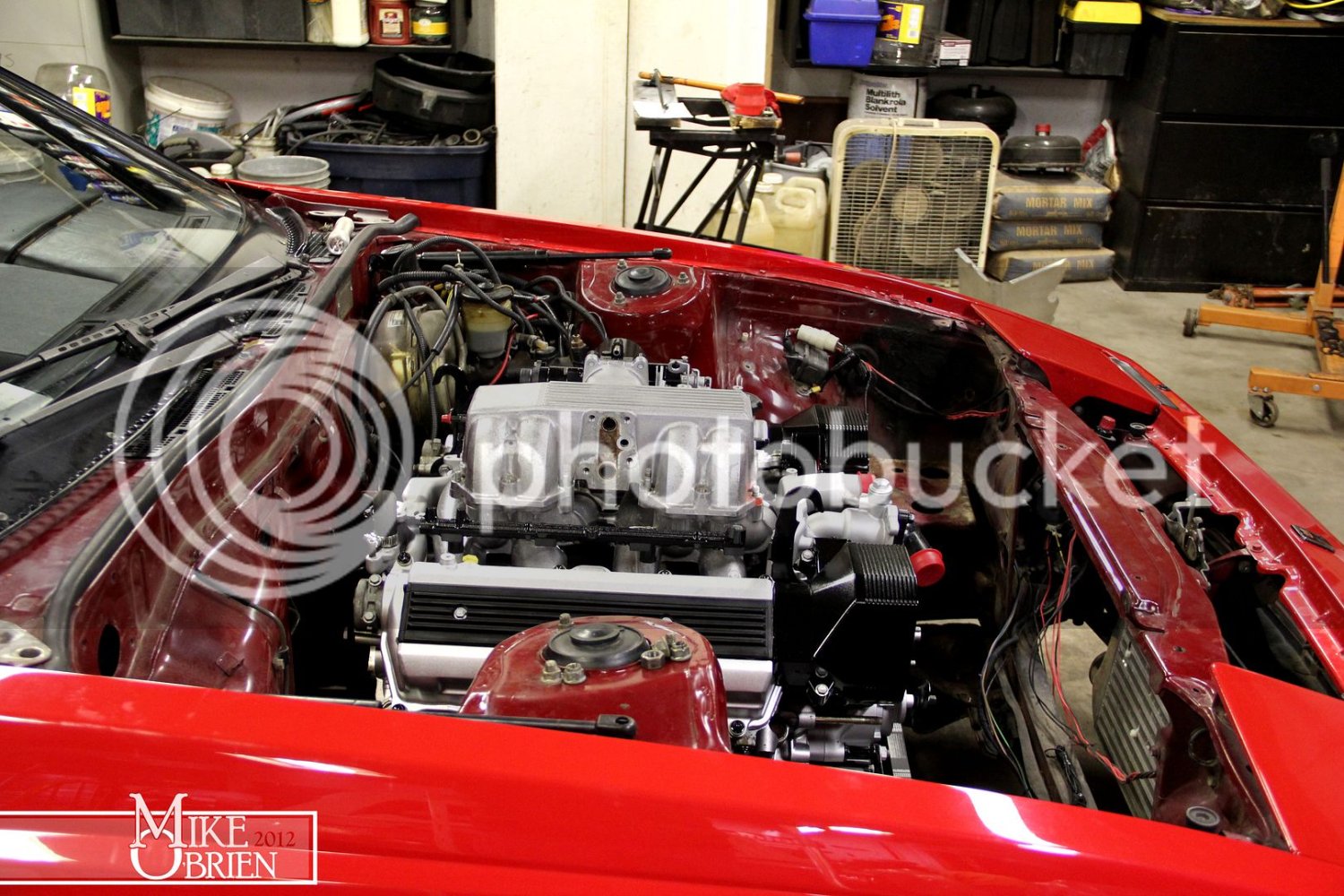
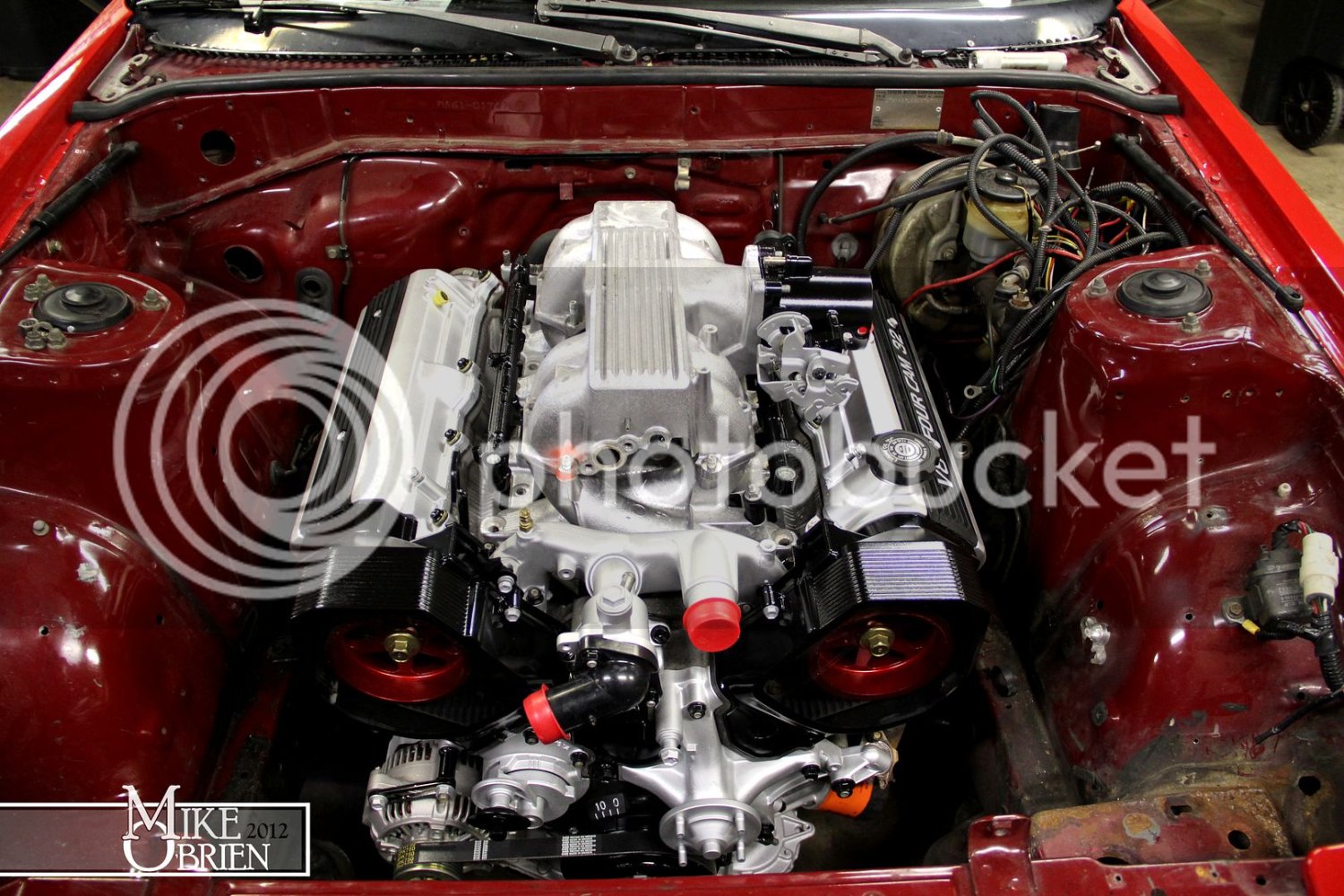
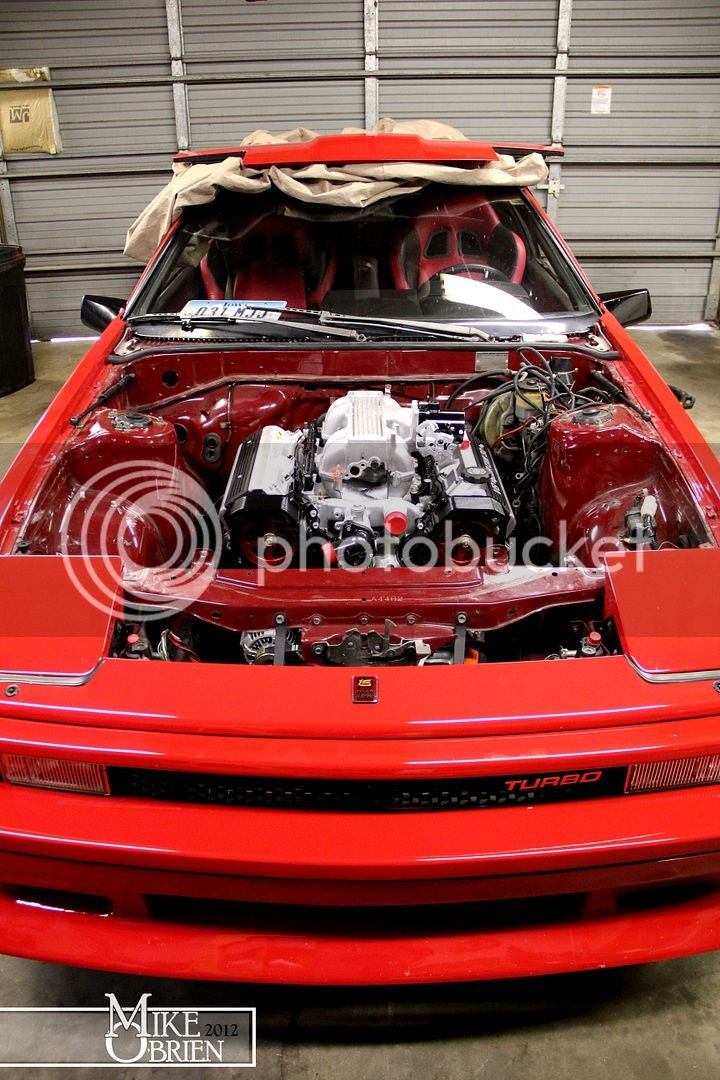
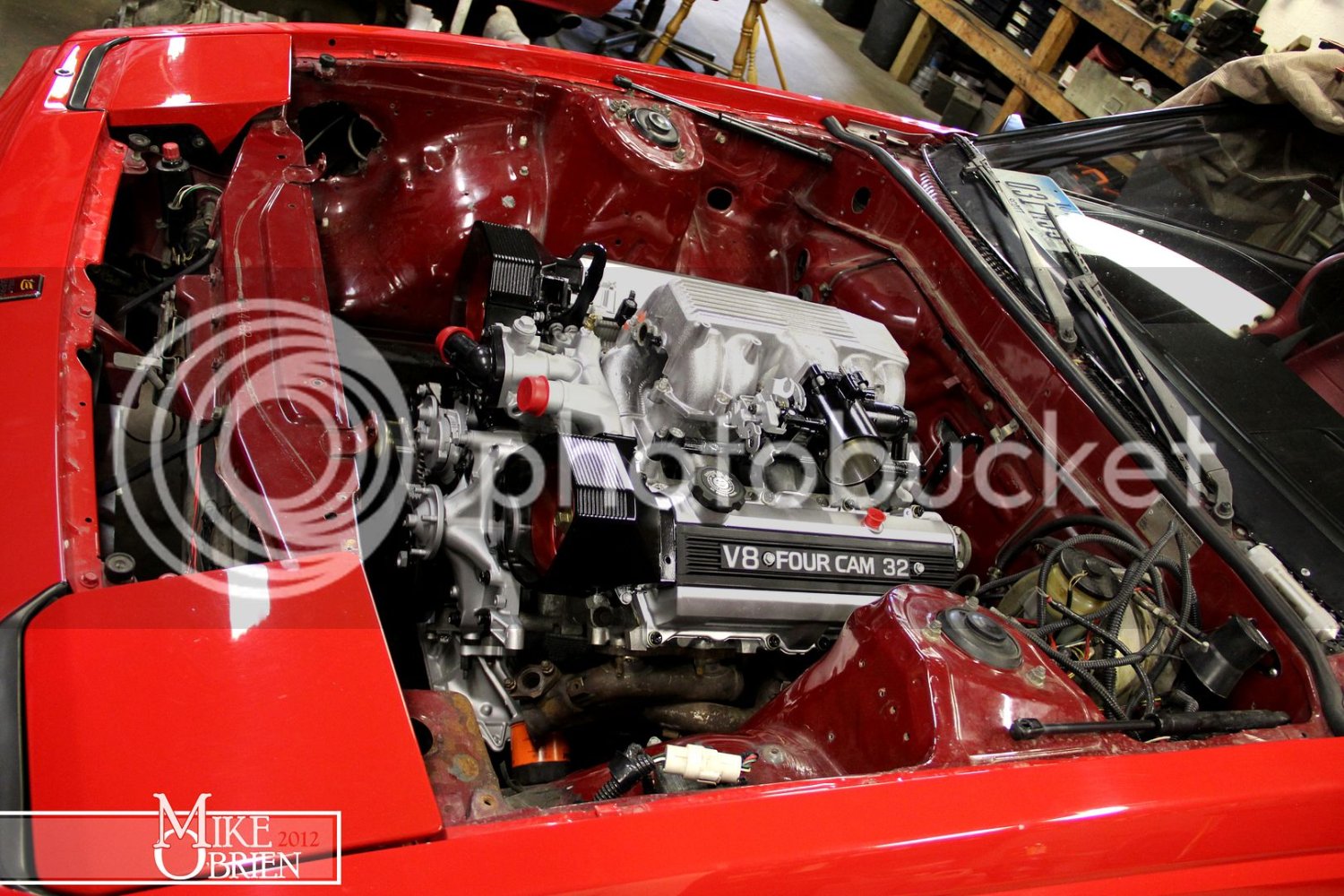
Clearance from the back of the heads to the firewall is around 4-5 inches:
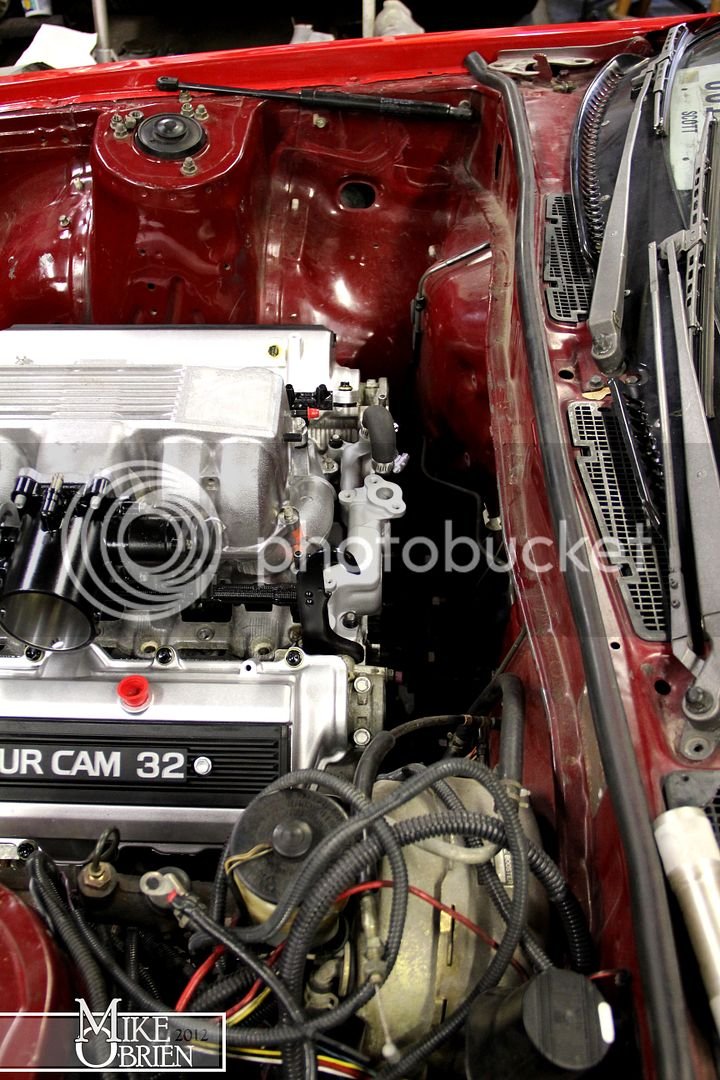
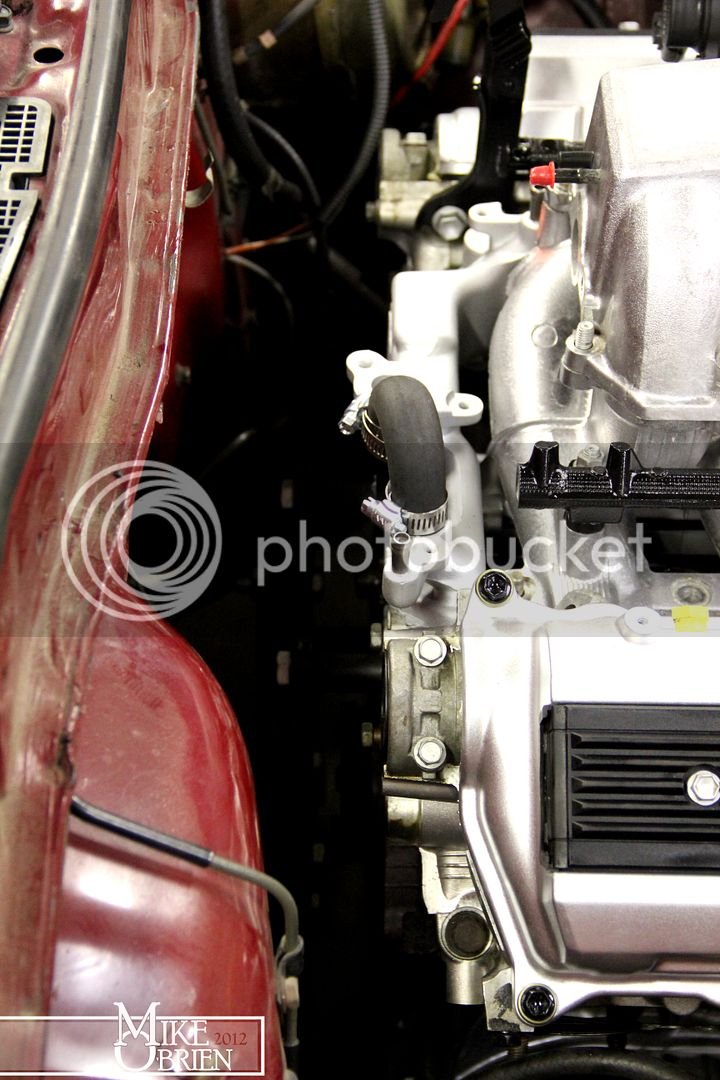
There was a surprising amount of room to work with around the manifolds and frame rails. The driver’s side cleared the steering shaft with the flipped manifolds easily, but is very close to the power steering lines to the steering gear. There was 3 inches of clearance from the lowest/widest valve cover mounting point to the brake proportioning valve on the driver's shock tower.
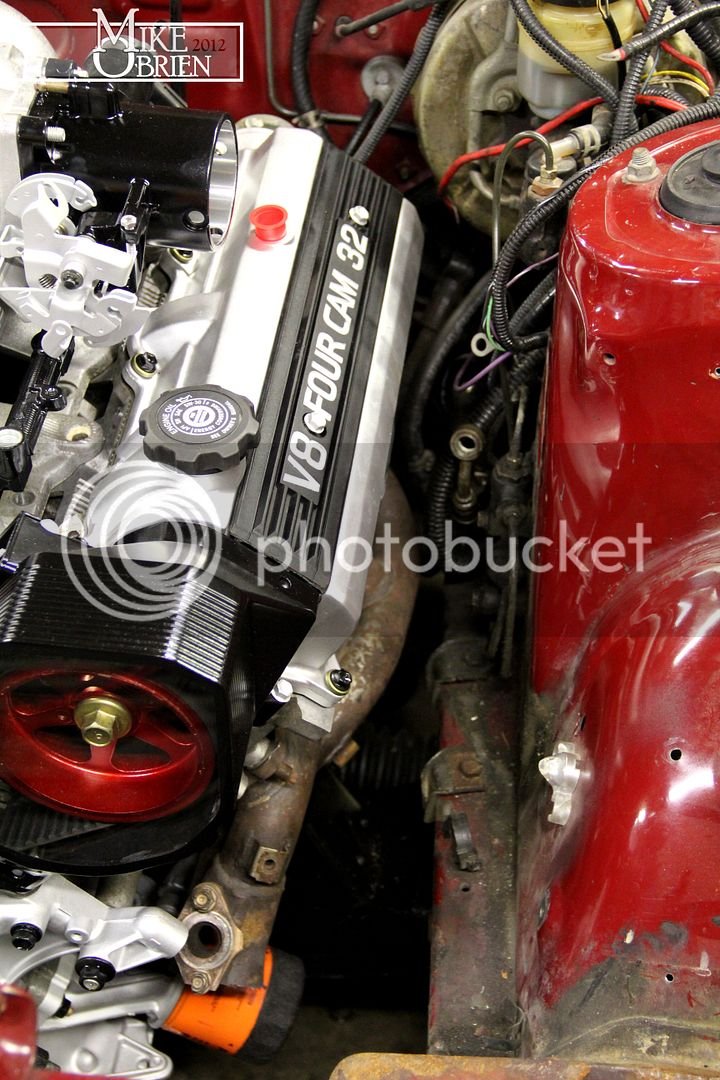
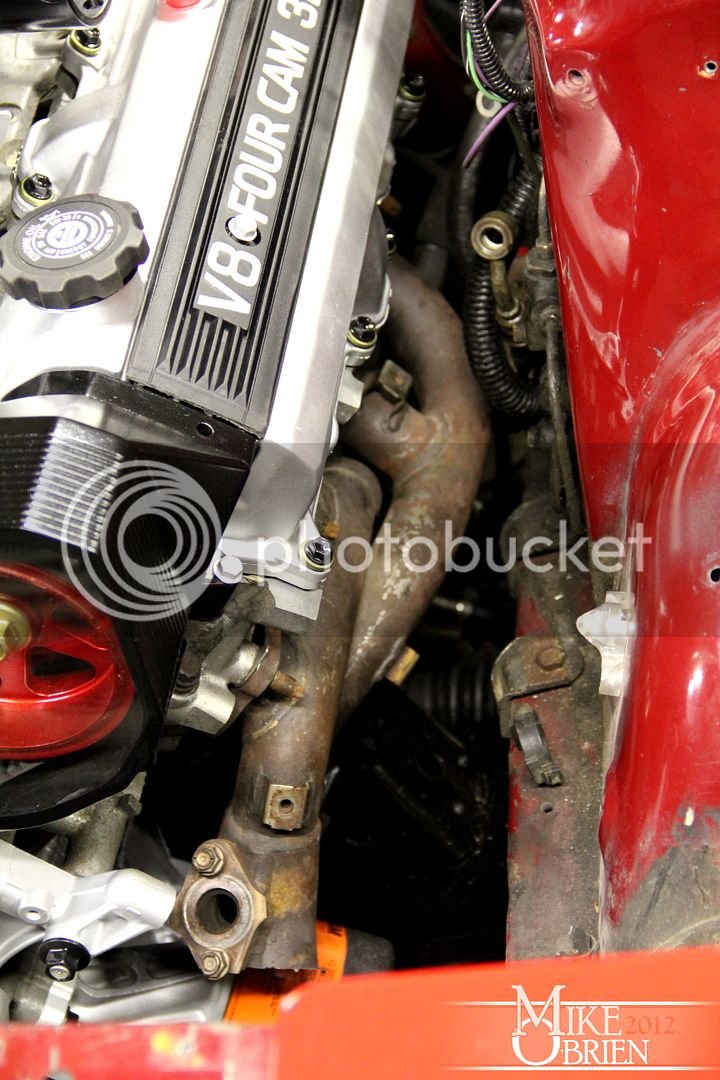
There was even enough room on the passenger side to install/remove the manifold without much fuss. There was 4 inches of clearance from the lowest/widest valve cover mounting point to the shock tower on the passenger side:
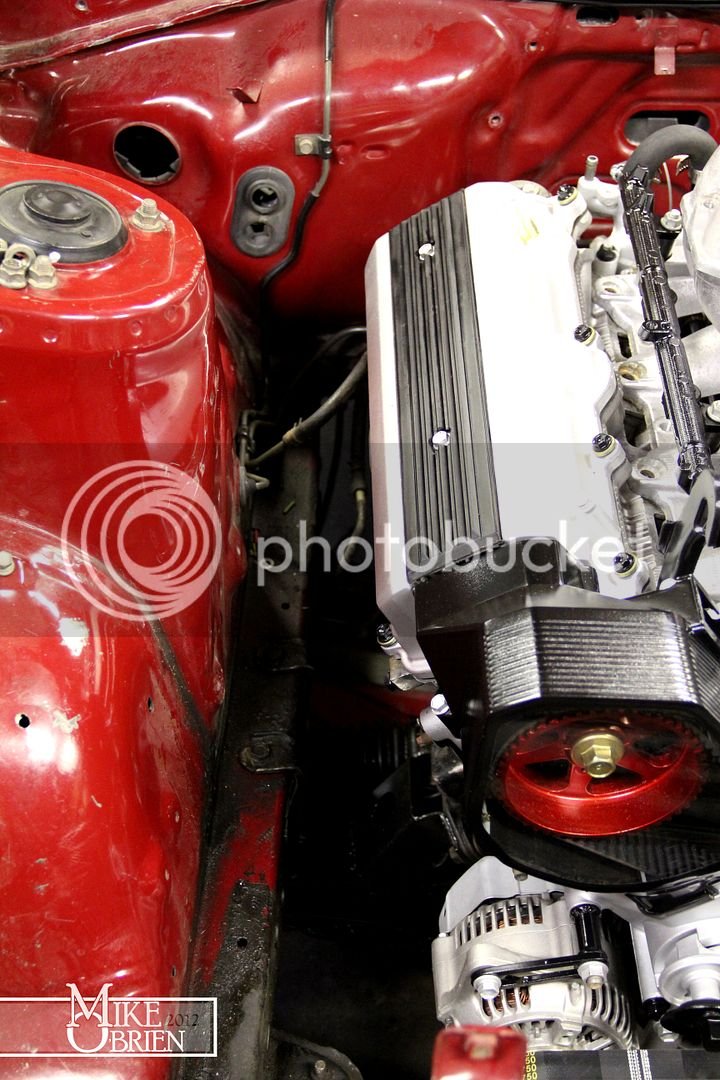
The obstructing primary was trimmed to re-fit the manifold for clearance checking.
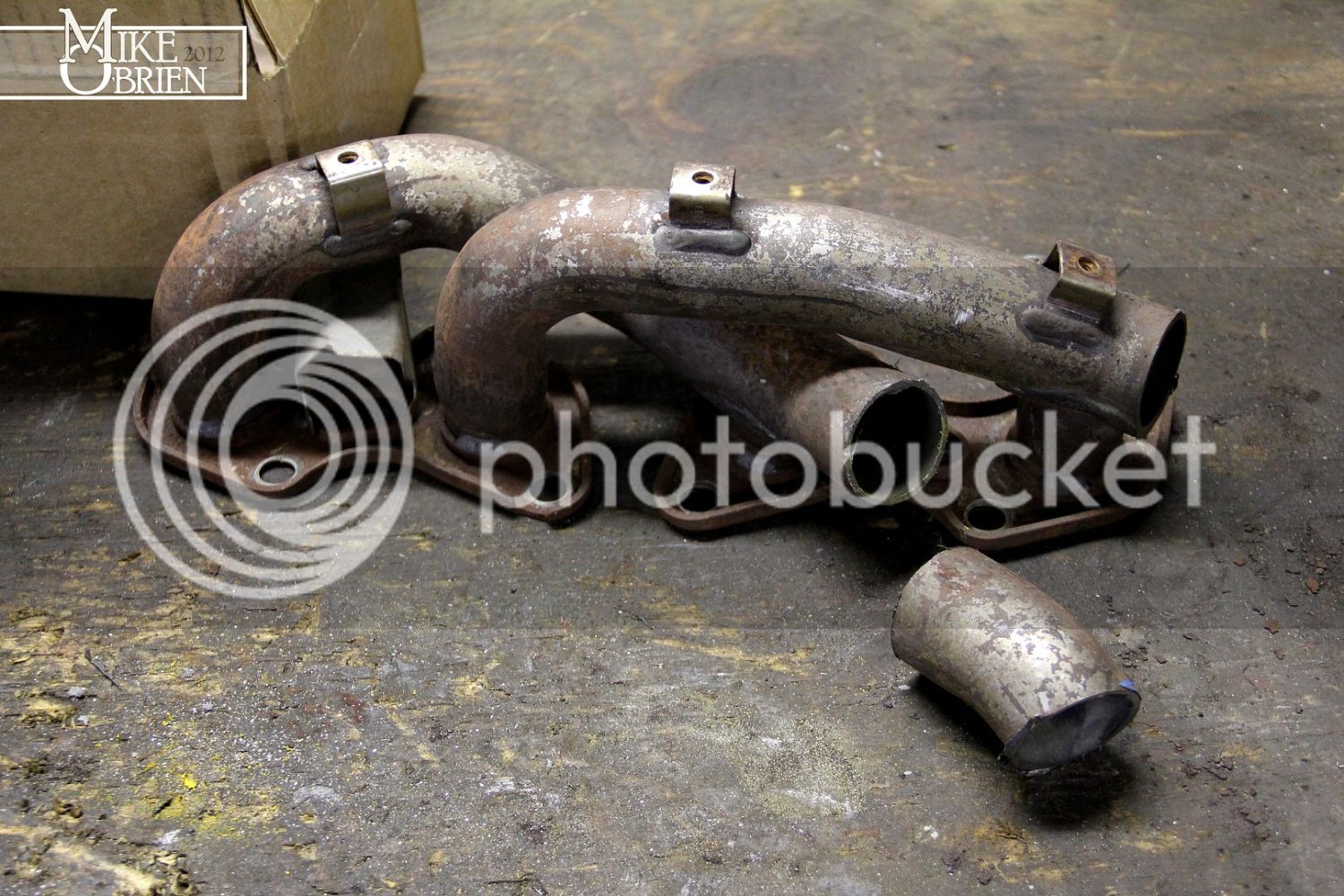
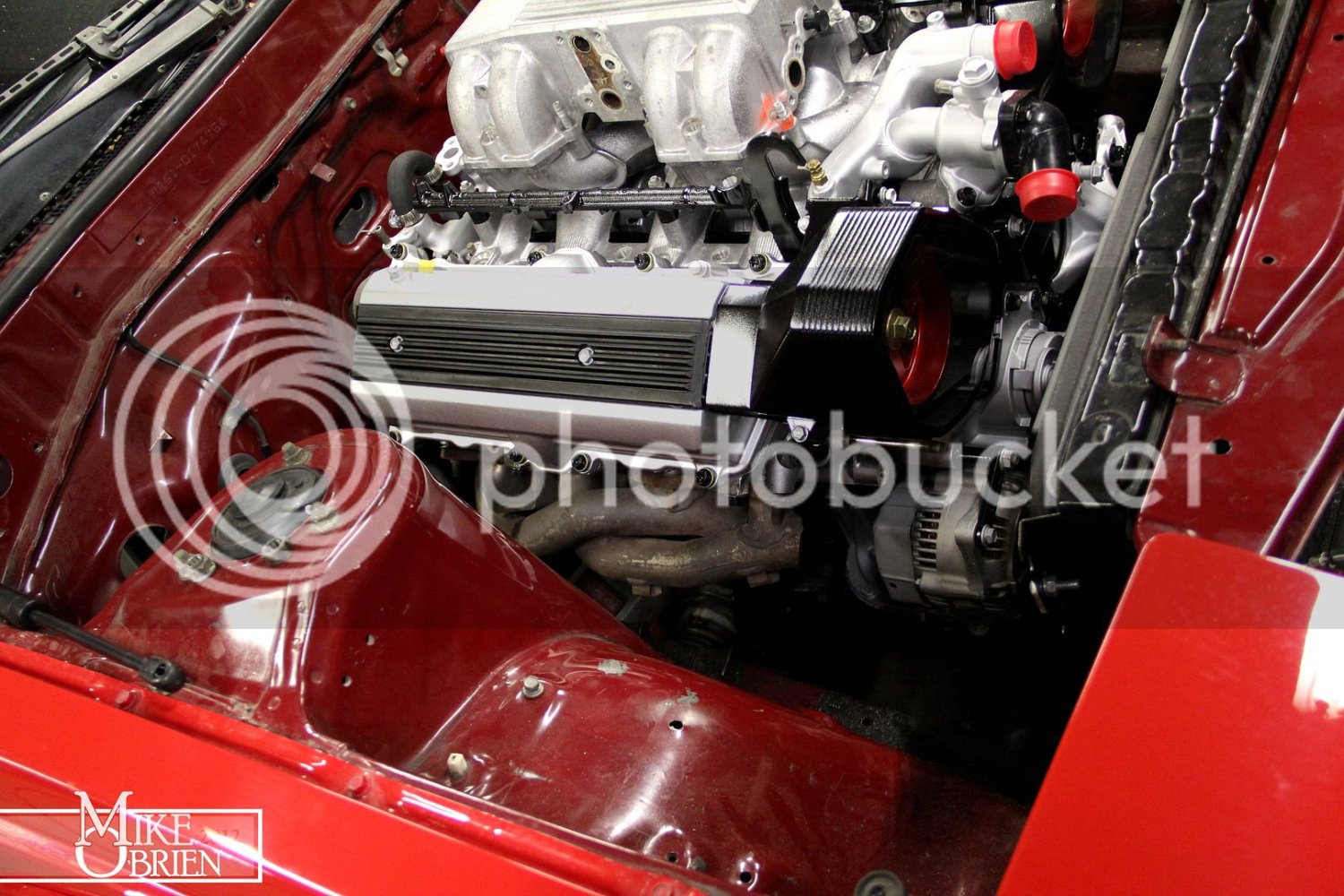
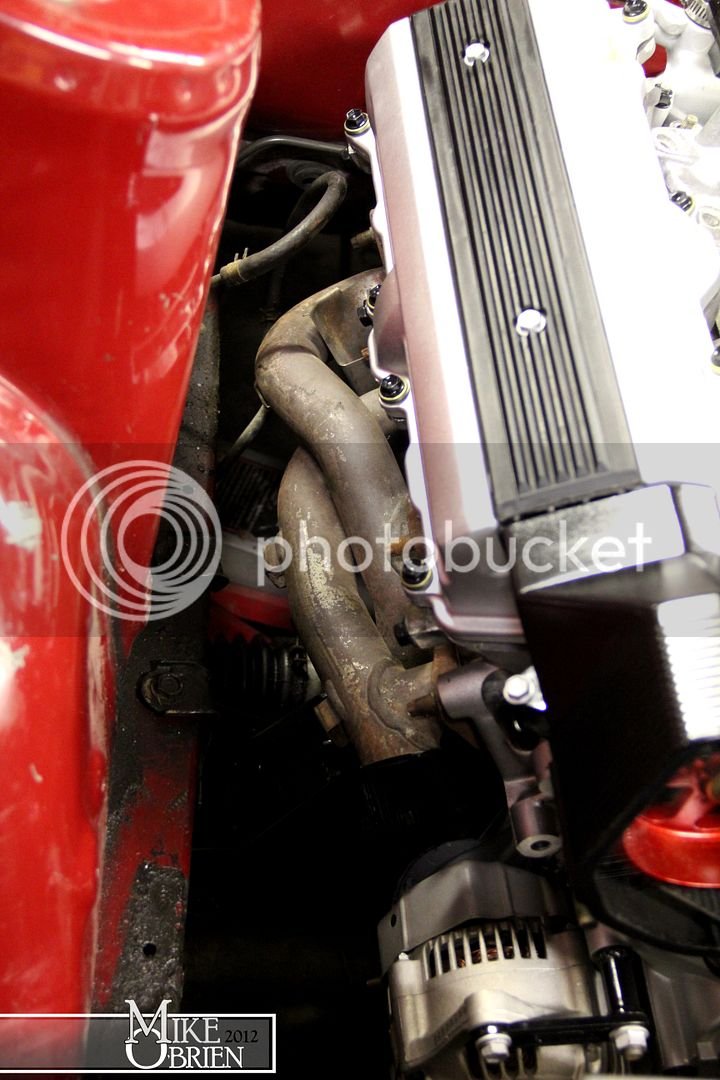
There was 6.5 inches of clearance from the radiator outlet to the radiator panel, and 7.5 inches from the alternator pulley to the radiator panel.
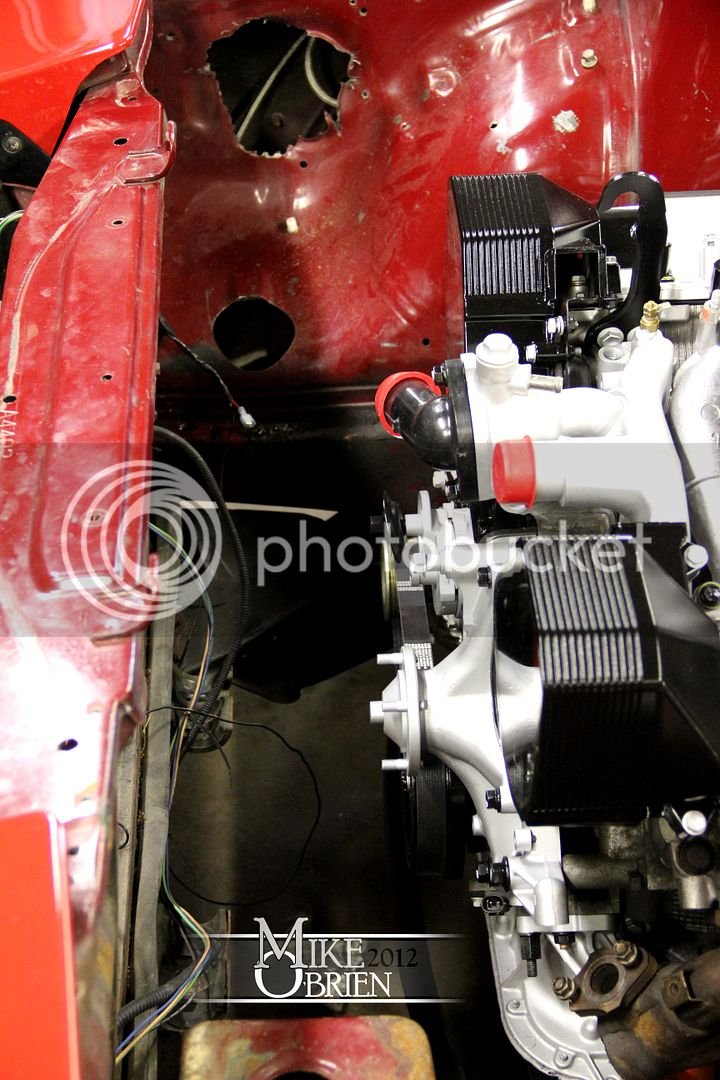
The old radiator and fans were quickly installed to judge space availability:
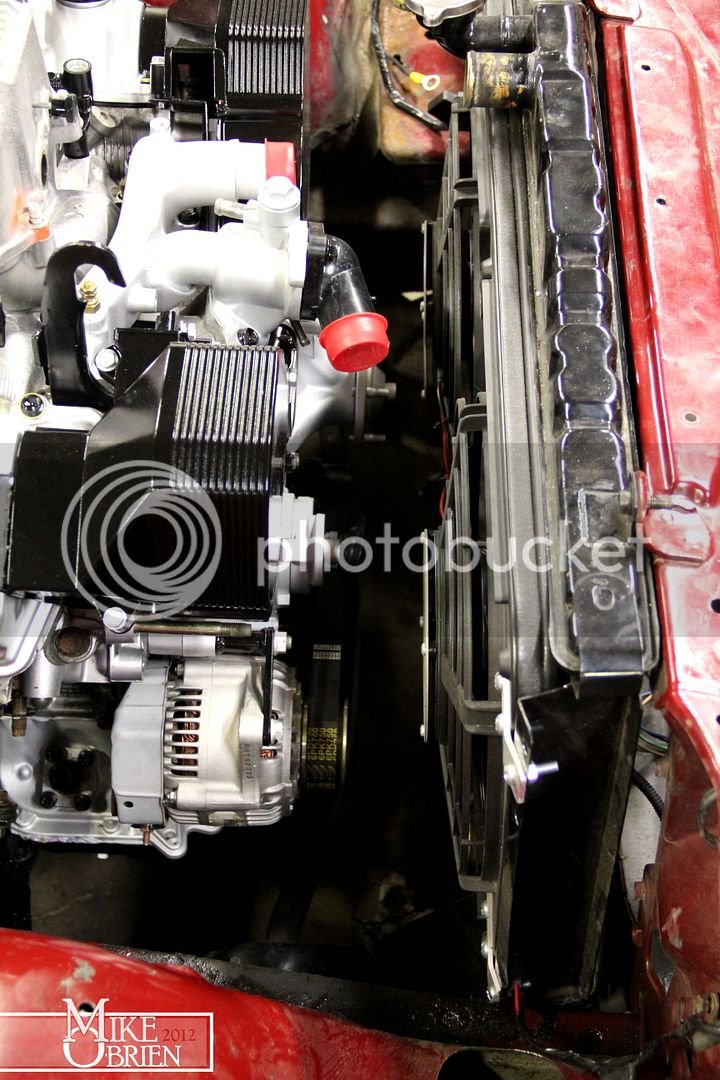
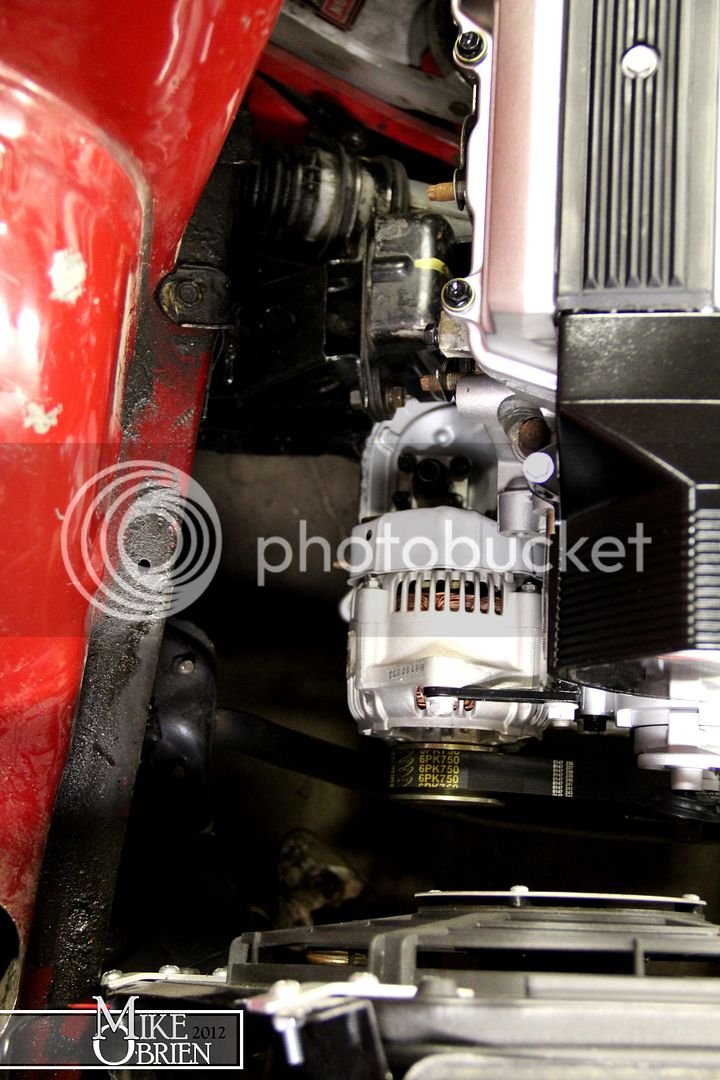
The turbo was also judged for the best possible placement. The passenger side allows the downpipe to move between the shock tower and valve cover (above the manifold) and exit down and through the side. There should be enough room for a wastegate, and all the needed turbo manifold piping/braces.
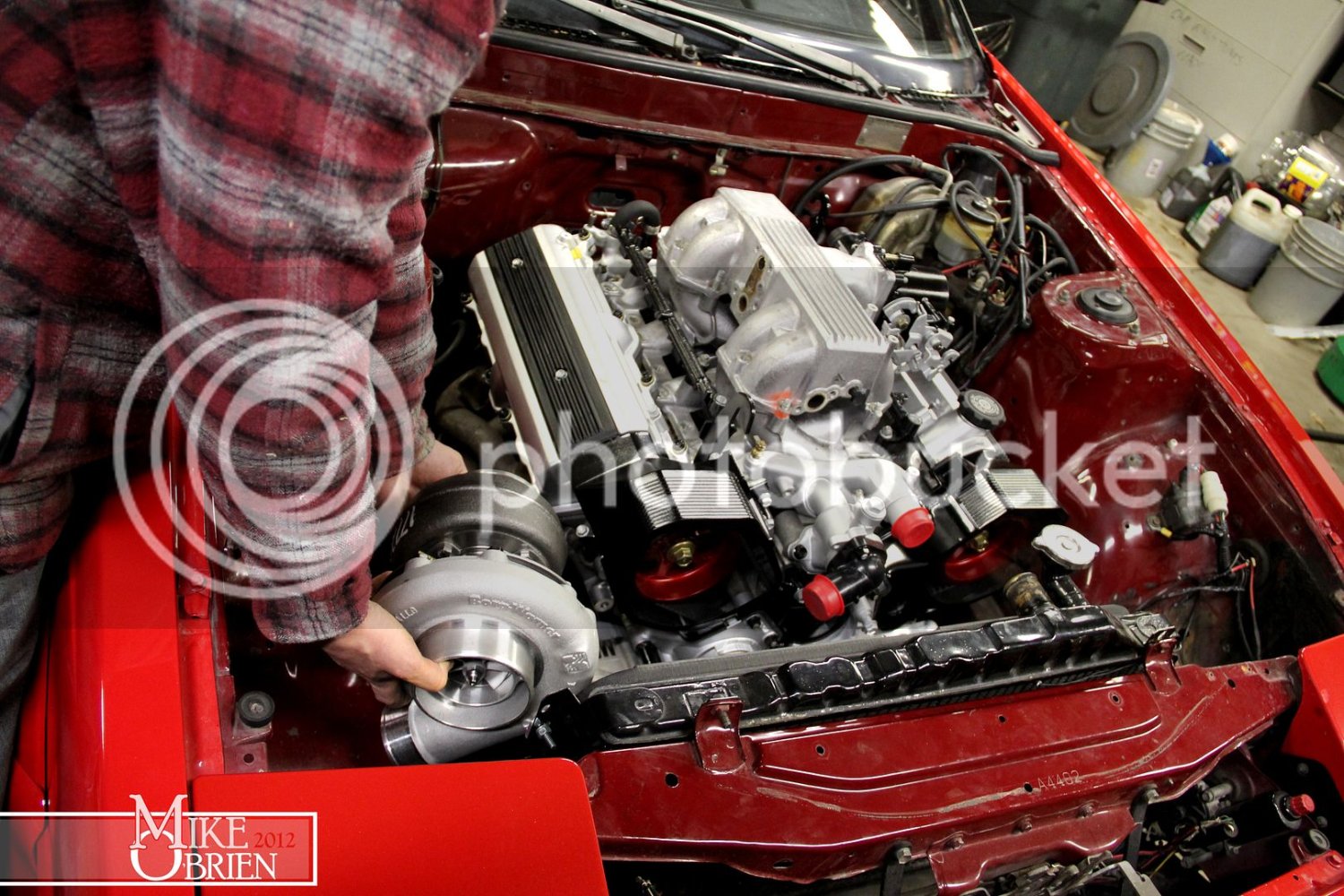
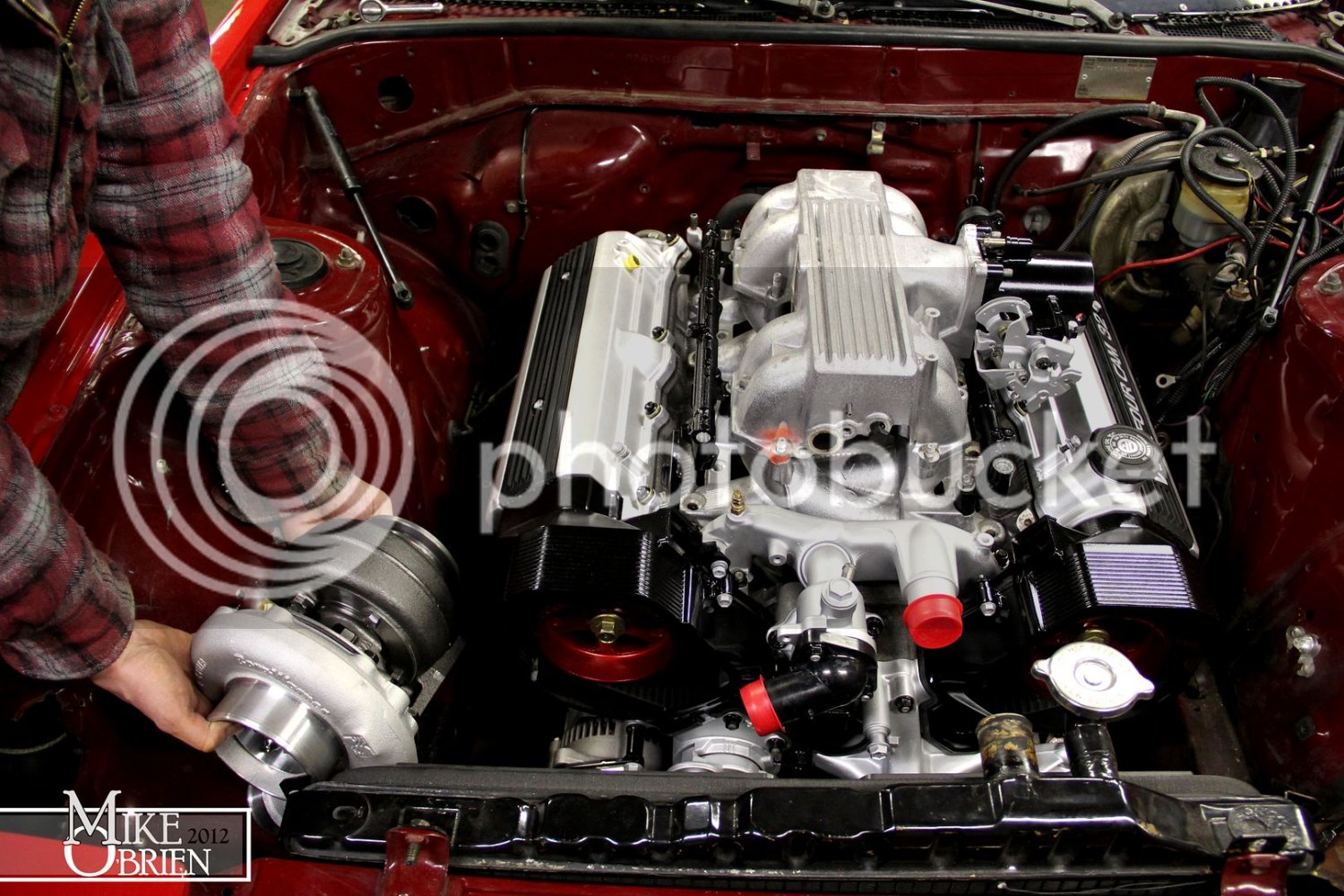
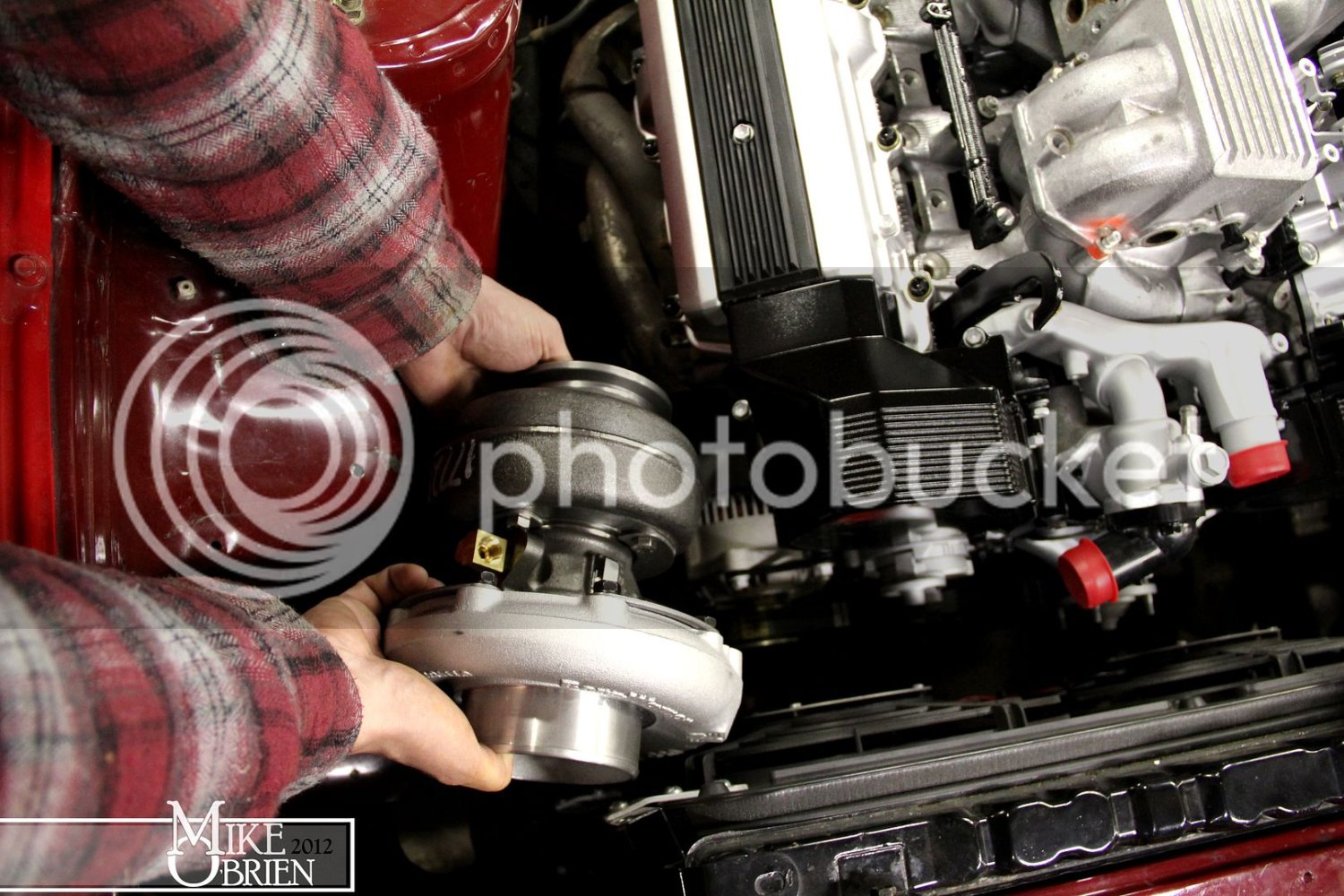
The hood closed with no issues with the manifold flipped around. I foresee no issues with clearance when the intercooler pipes are fabricated and mounted.
I am now thinking about what to do for a radiator. The driver's manifold needs a pipe to route to the passenger merge location, and I am worried about the lower rad hose outlet interfering with accessible routing. Also, I am worried about thicker aluminum radiators pushing the fans out even further and choking space up front.
I thought about mounting a radiator underneath the rad panel, but decided that was not the way to go since no viable options are there for inlets/outlets in an appropriate size. (Would need a 24”x14” radiator with suitable inlet/outlet) As of now, the Griffin 25241 looks like what I will go with. It is only 15.5 inches tall, which will allow it to sit a bit further in compared to the stock MKII radiator. Also, the cross flow inlet/outlets will better position the lower inlet to escape the driver's exhaust section.
http://www.summitracing.com/parts/GRI-1-25241-X/
I did alot of measuring and calculations, and I think I can actually fit the radiator (with a tiny bit of trimming on the rad panel) so that the fans will give a bit more clearance than what is currently available with the stock radiator.
More to come soon. Parts are coming in a steady flow, so lots of more projects should start springing up in the near future.
Thanks, -Mike
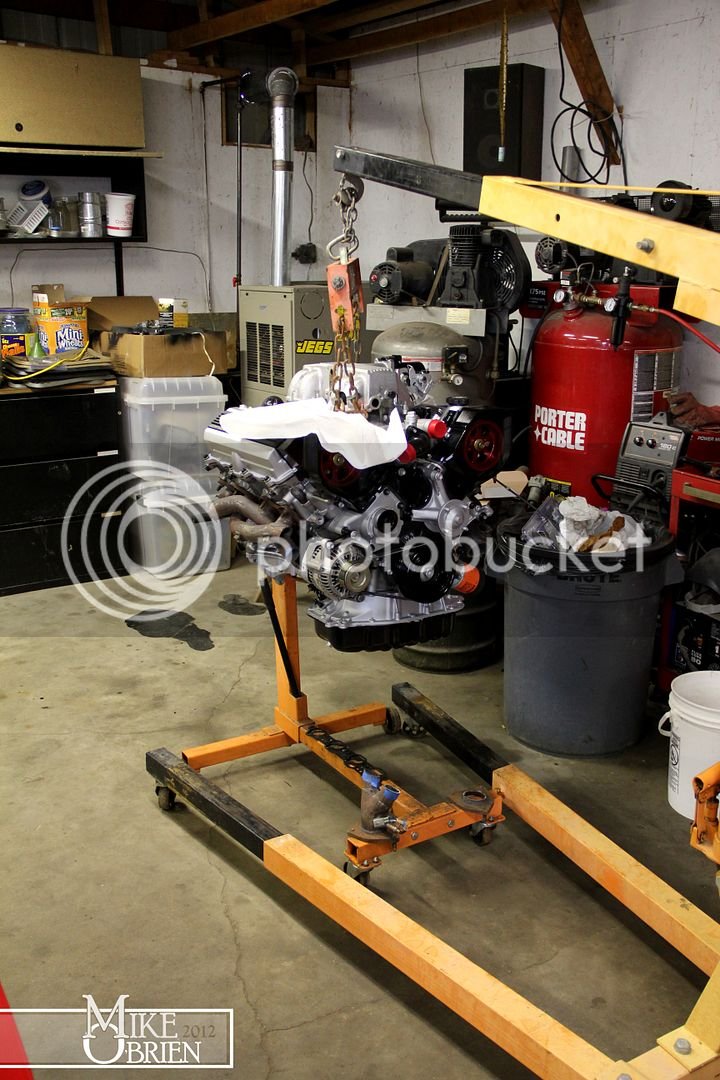
I had to dig around for my old set of lower mounts, and found it easiest to mount the lowers to the uppers after seeing that one of the passenger manifold's (flipped driver's manifold) primaries was contacting the lower mount and preventing them from mating.
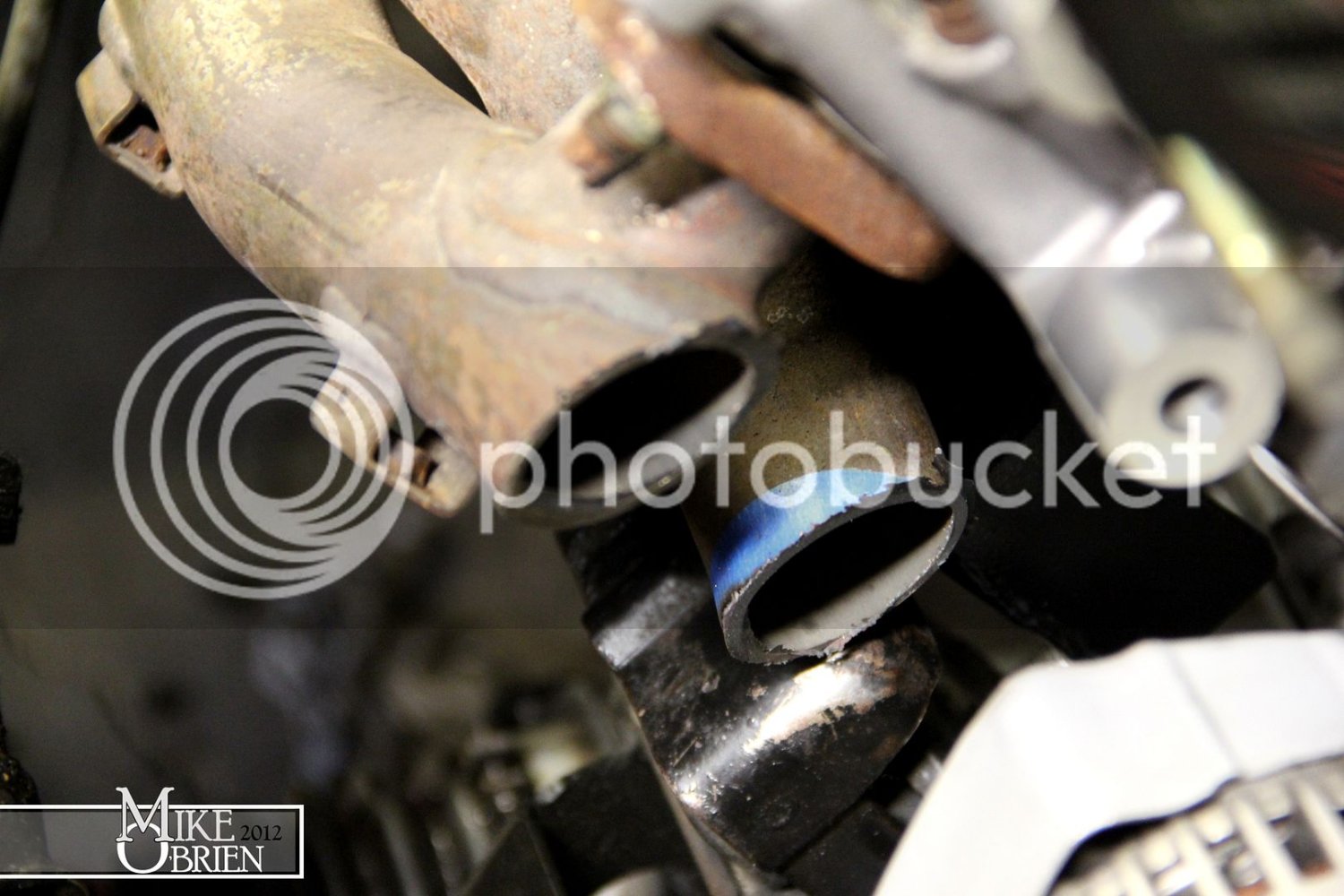
I removed the passenger manifold, and set the engine on its perches.
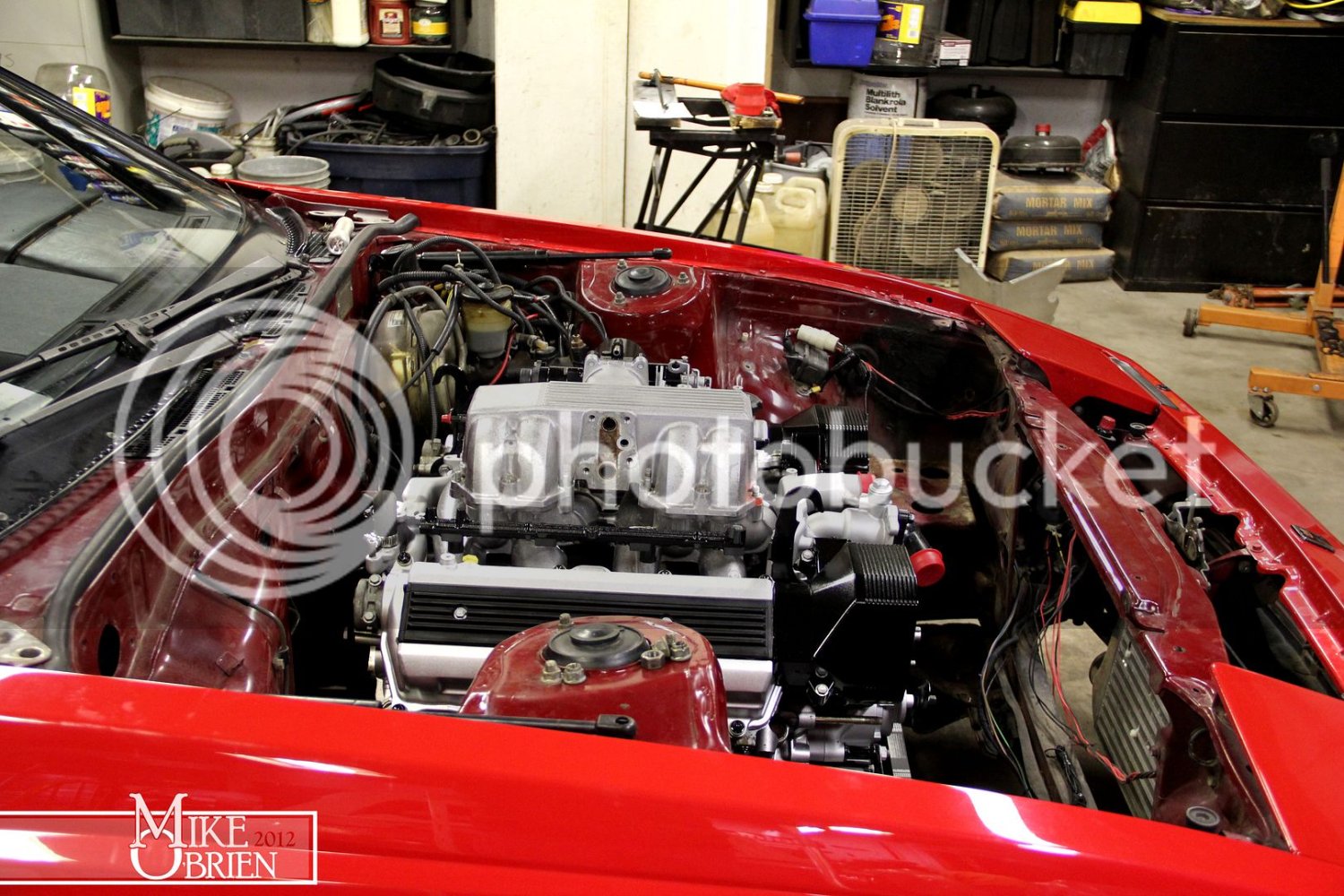
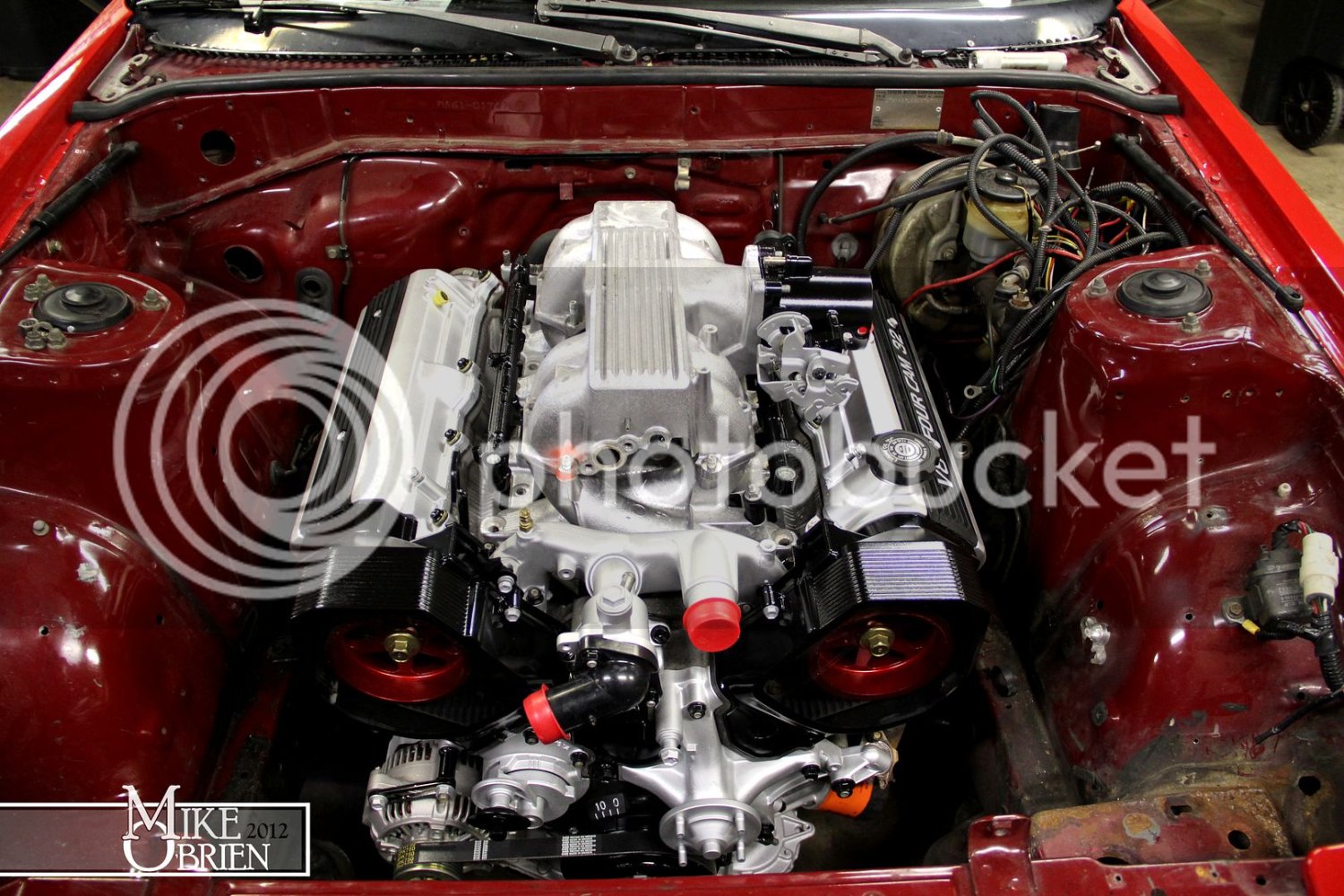
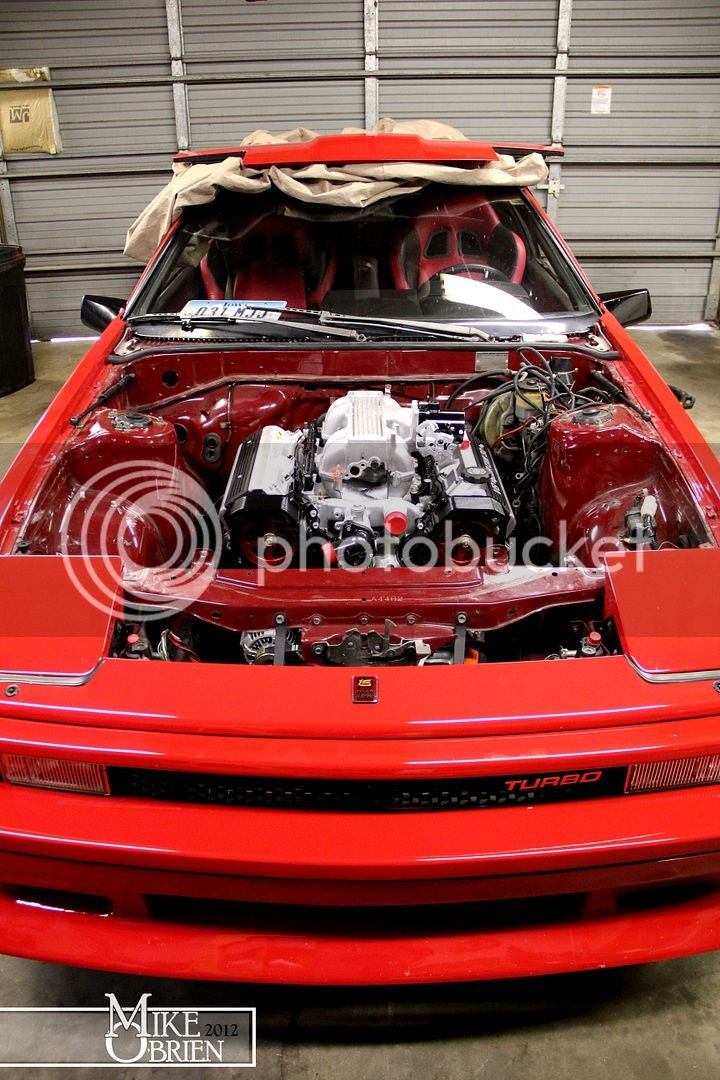
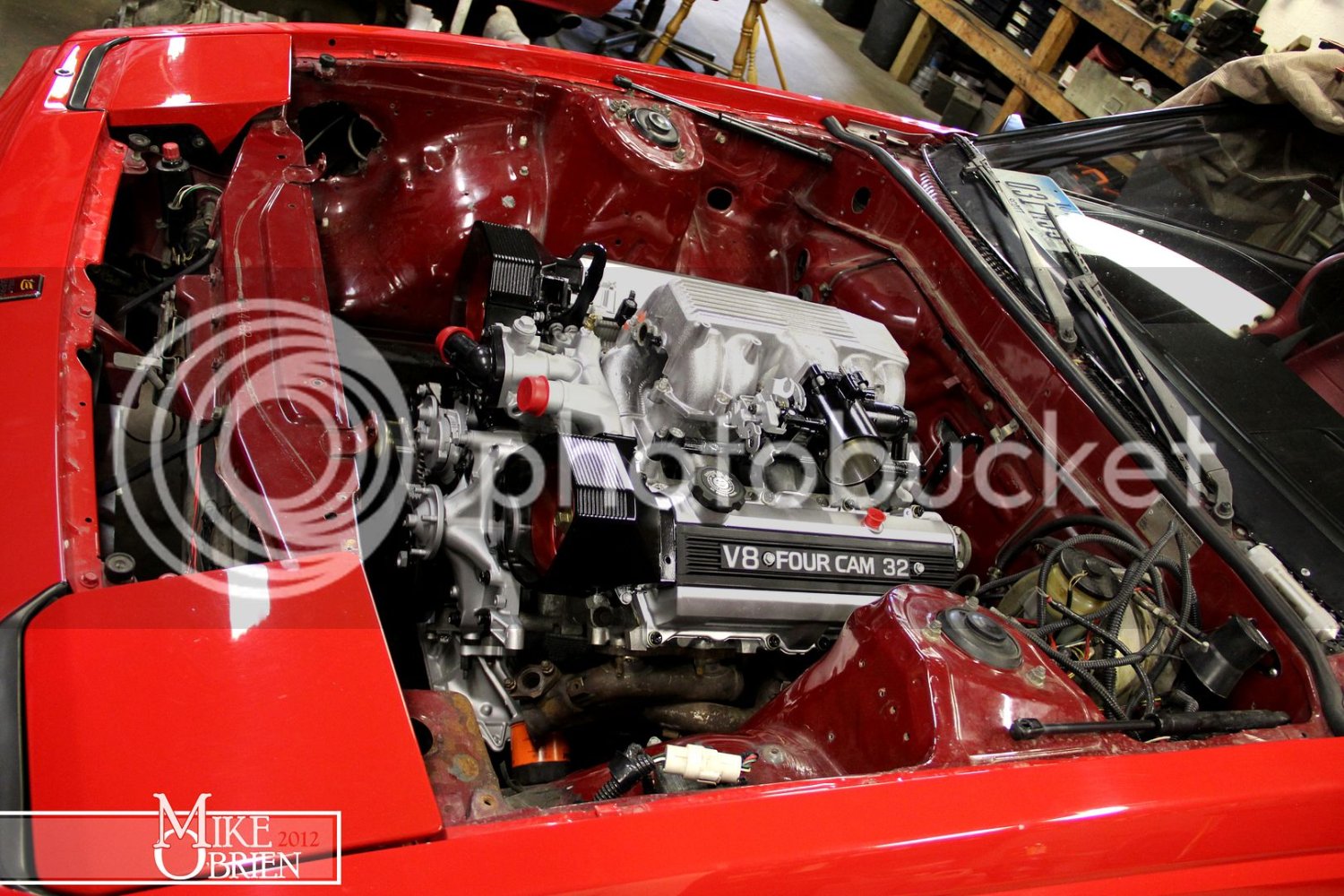
Clearance from the back of the heads to the firewall is around 4-5 inches:
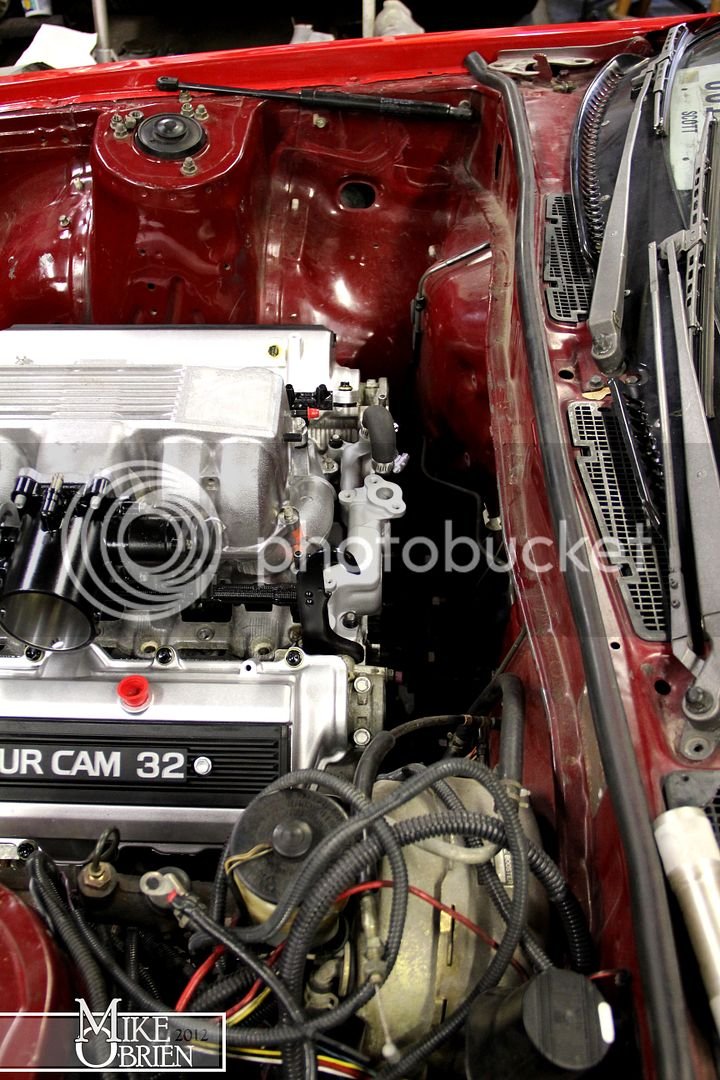
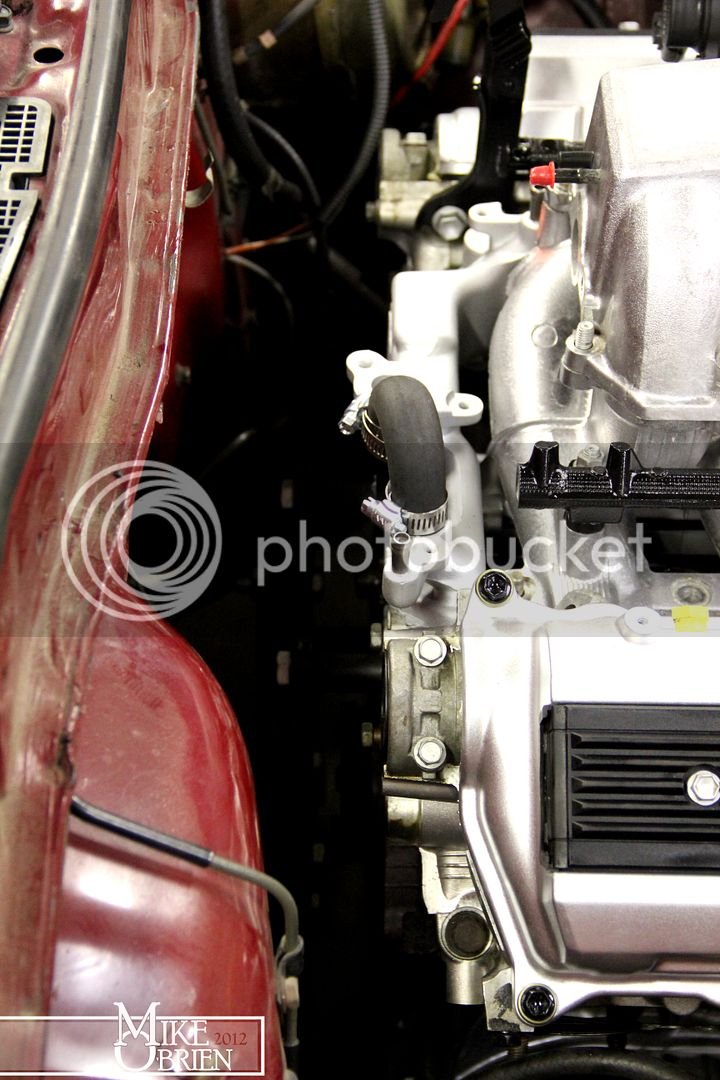
There was a surprising amount of room to work with around the manifolds and frame rails. The driver’s side cleared the steering shaft with the flipped manifolds easily, but is very close to the power steering lines to the steering gear. There was 3 inches of clearance from the lowest/widest valve cover mounting point to the brake proportioning valve on the driver's shock tower.
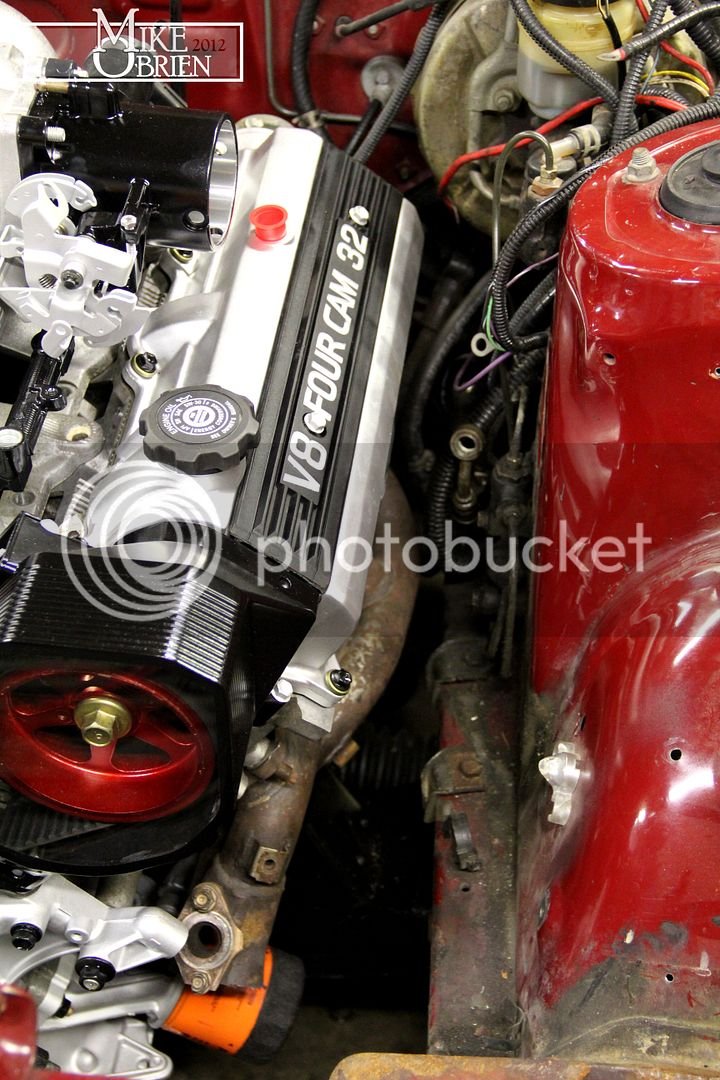
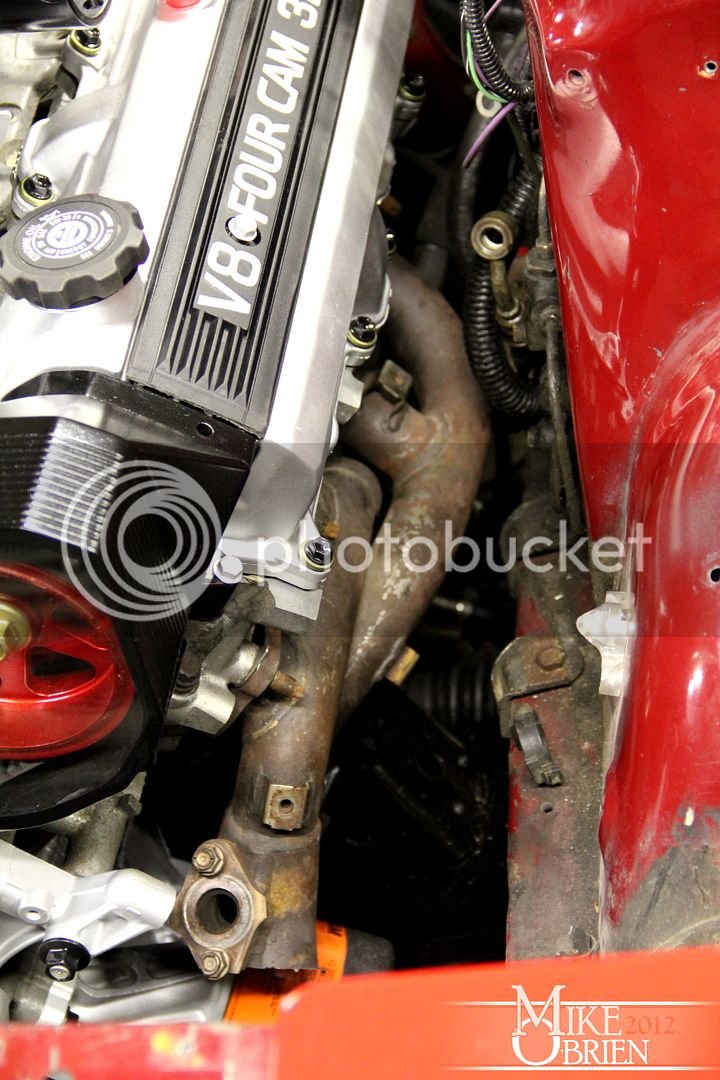
There was even enough room on the passenger side to install/remove the manifold without much fuss. There was 4 inches of clearance from the lowest/widest valve cover mounting point to the shock tower on the passenger side:
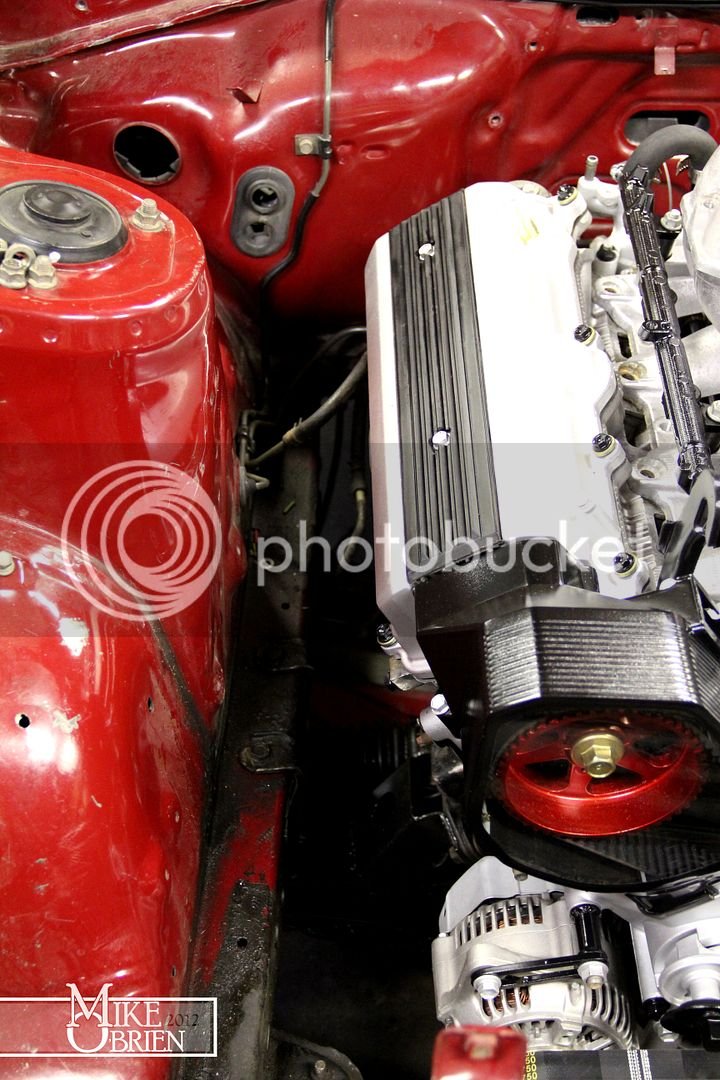
The obstructing primary was trimmed to re-fit the manifold for clearance checking.
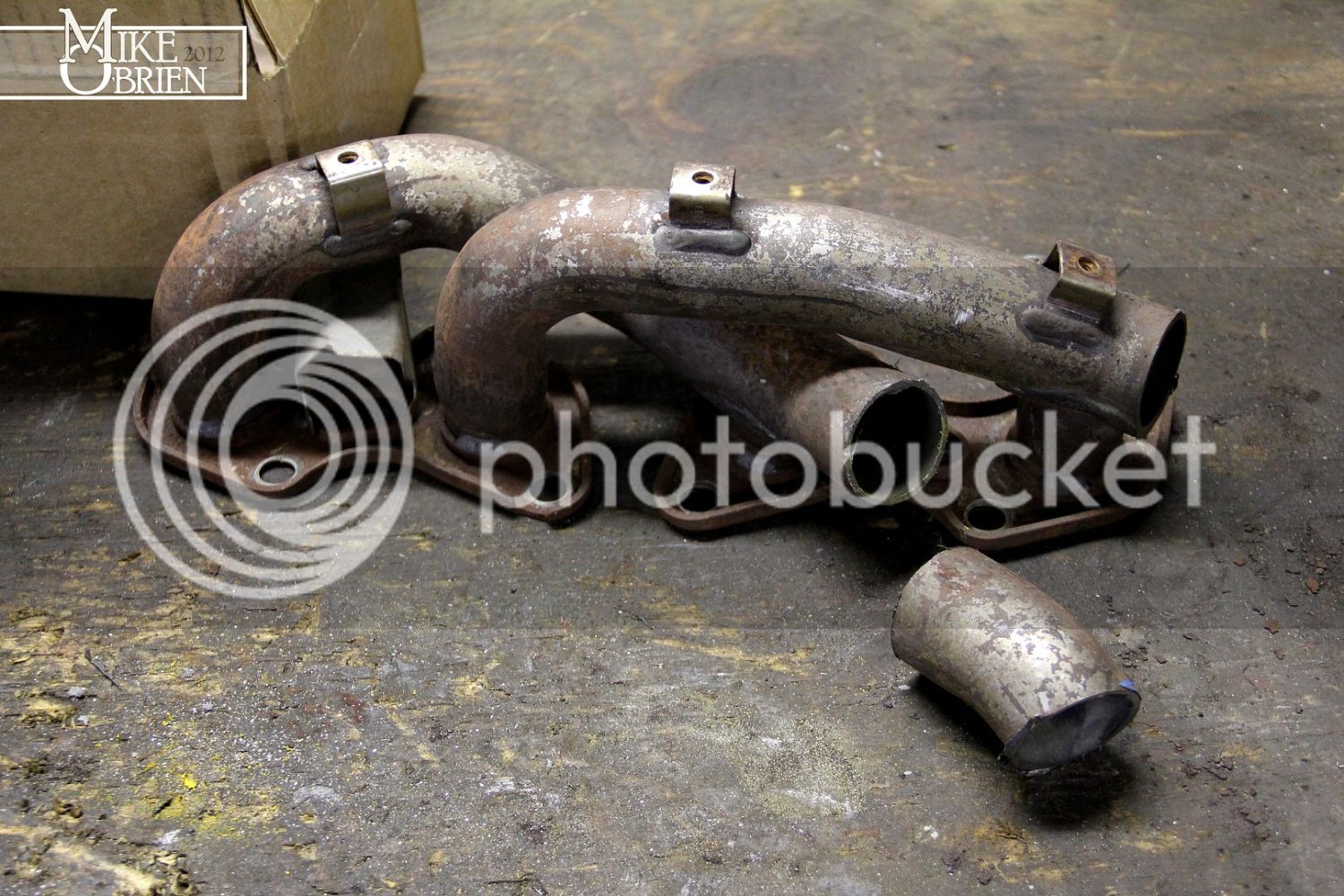
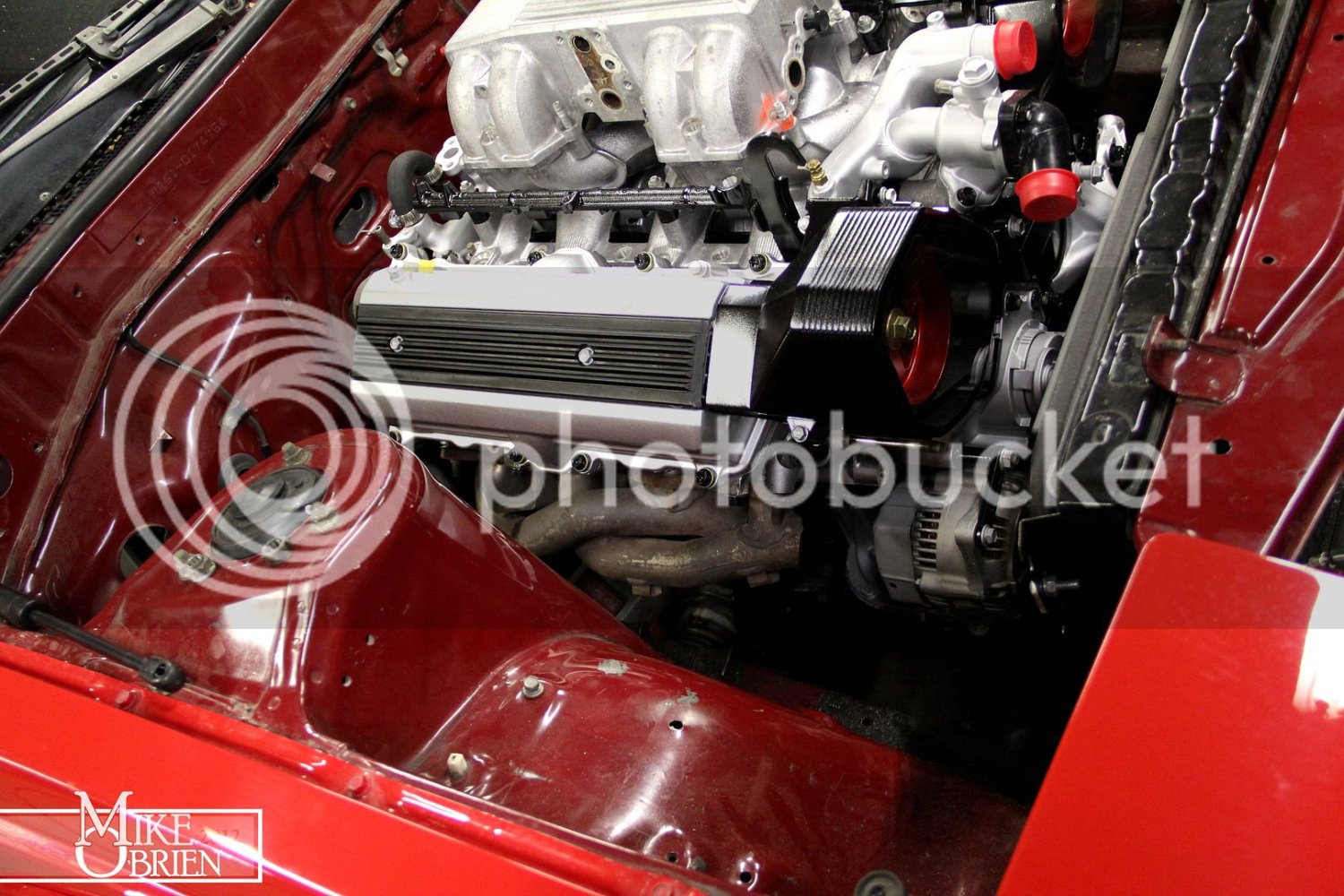
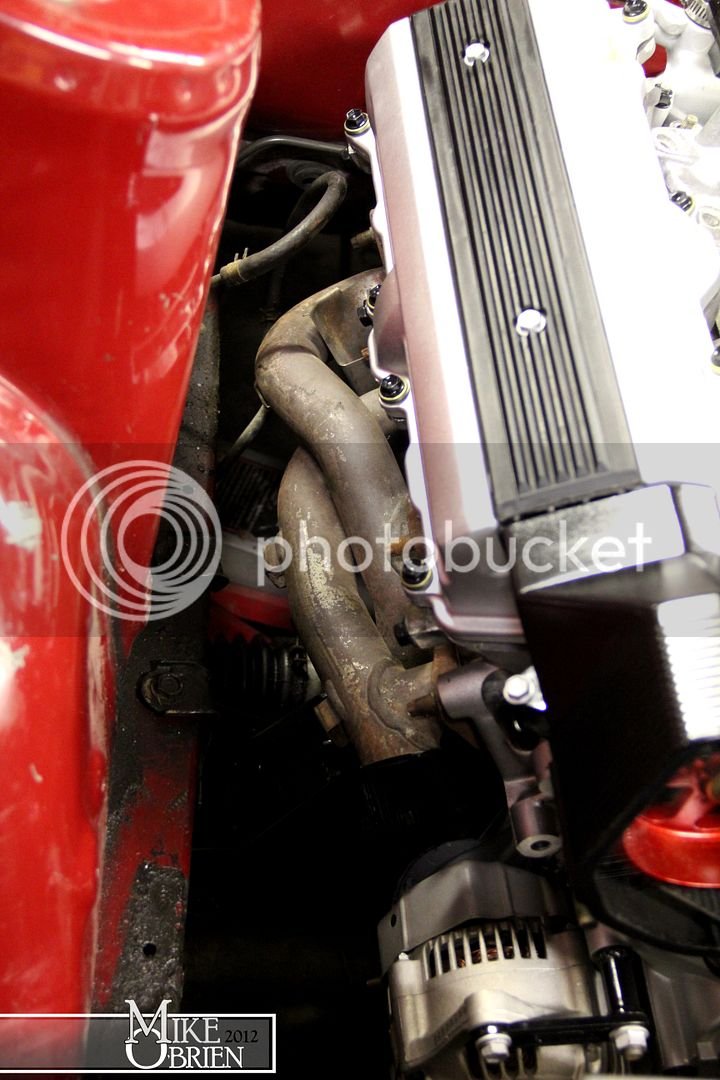
There was 6.5 inches of clearance from the radiator outlet to the radiator panel, and 7.5 inches from the alternator pulley to the radiator panel.
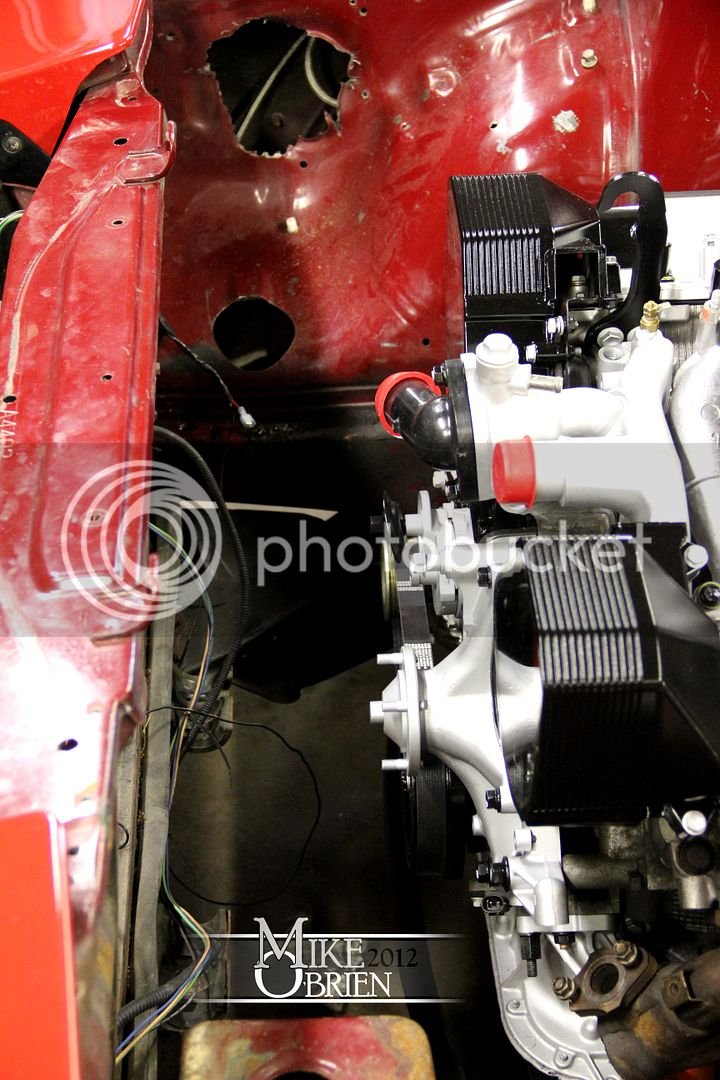
The old radiator and fans were quickly installed to judge space availability:
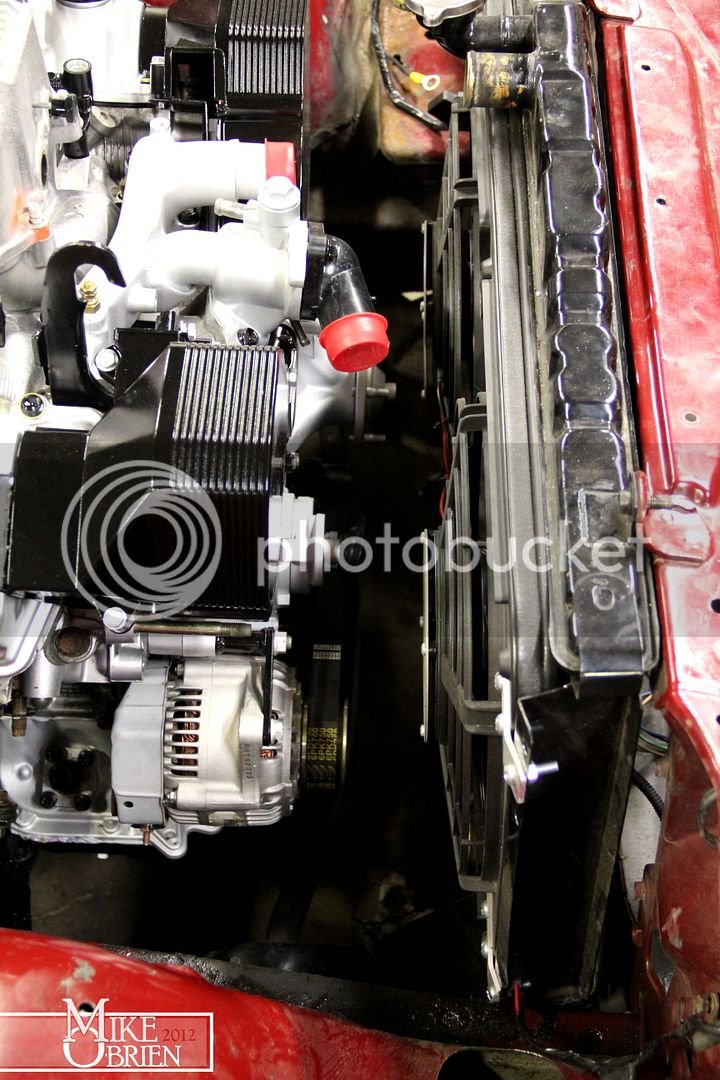
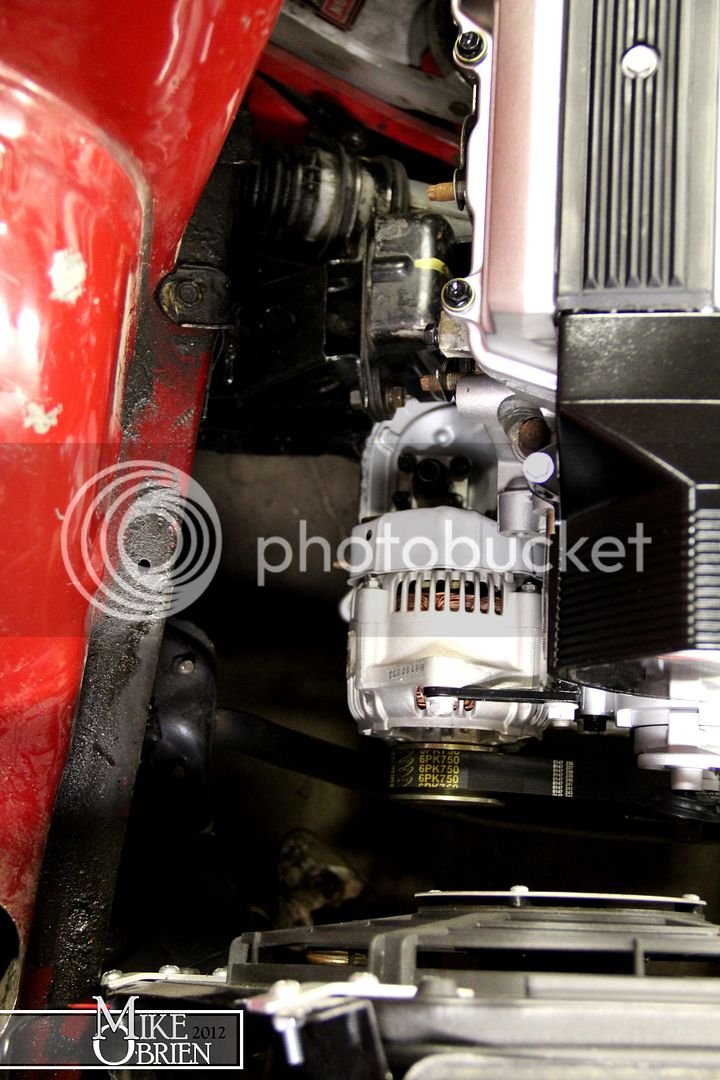
The turbo was also judged for the best possible placement. The passenger side allows the downpipe to move between the shock tower and valve cover (above the manifold) and exit down and through the side. There should be enough room for a wastegate, and all the needed turbo manifold piping/braces.
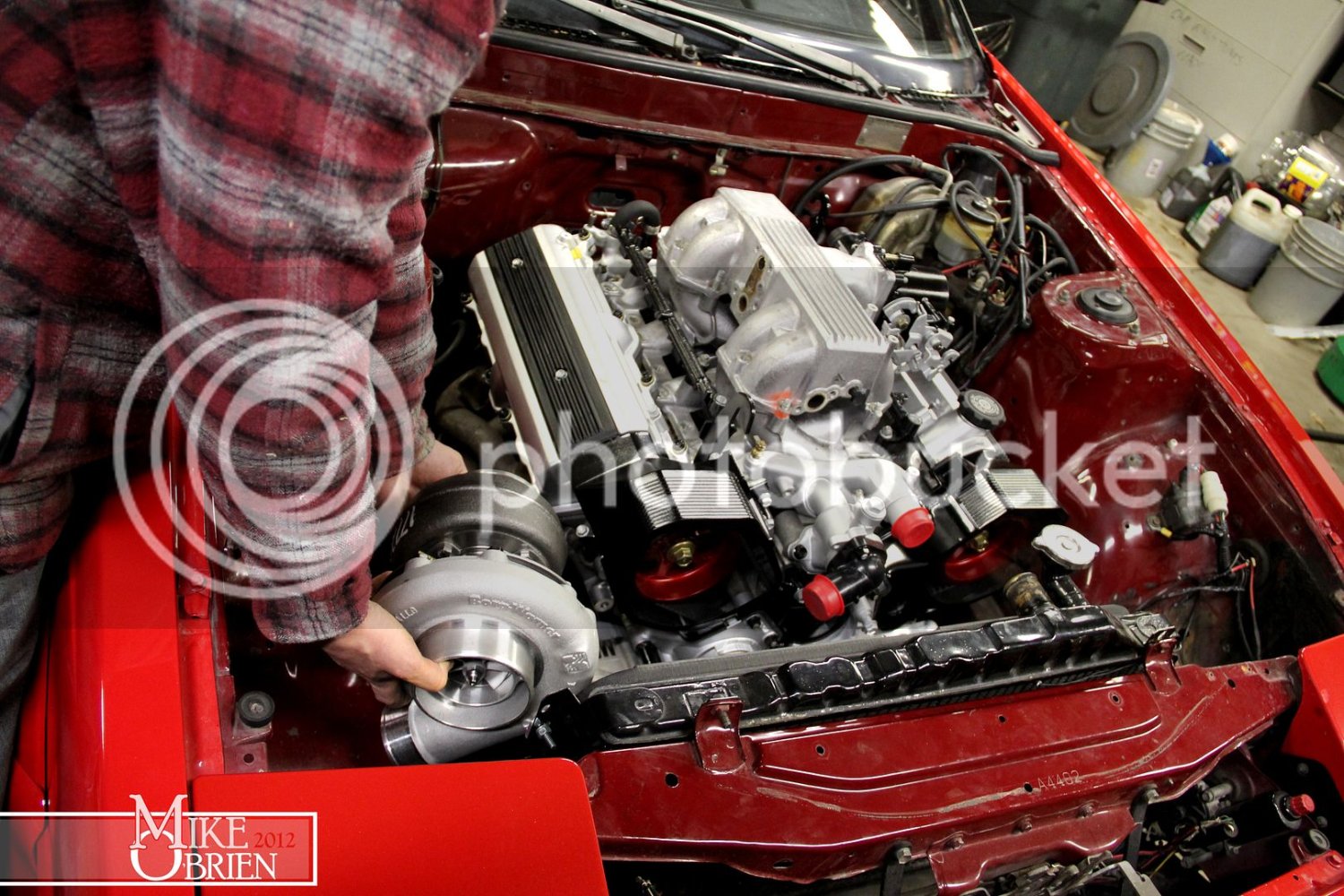
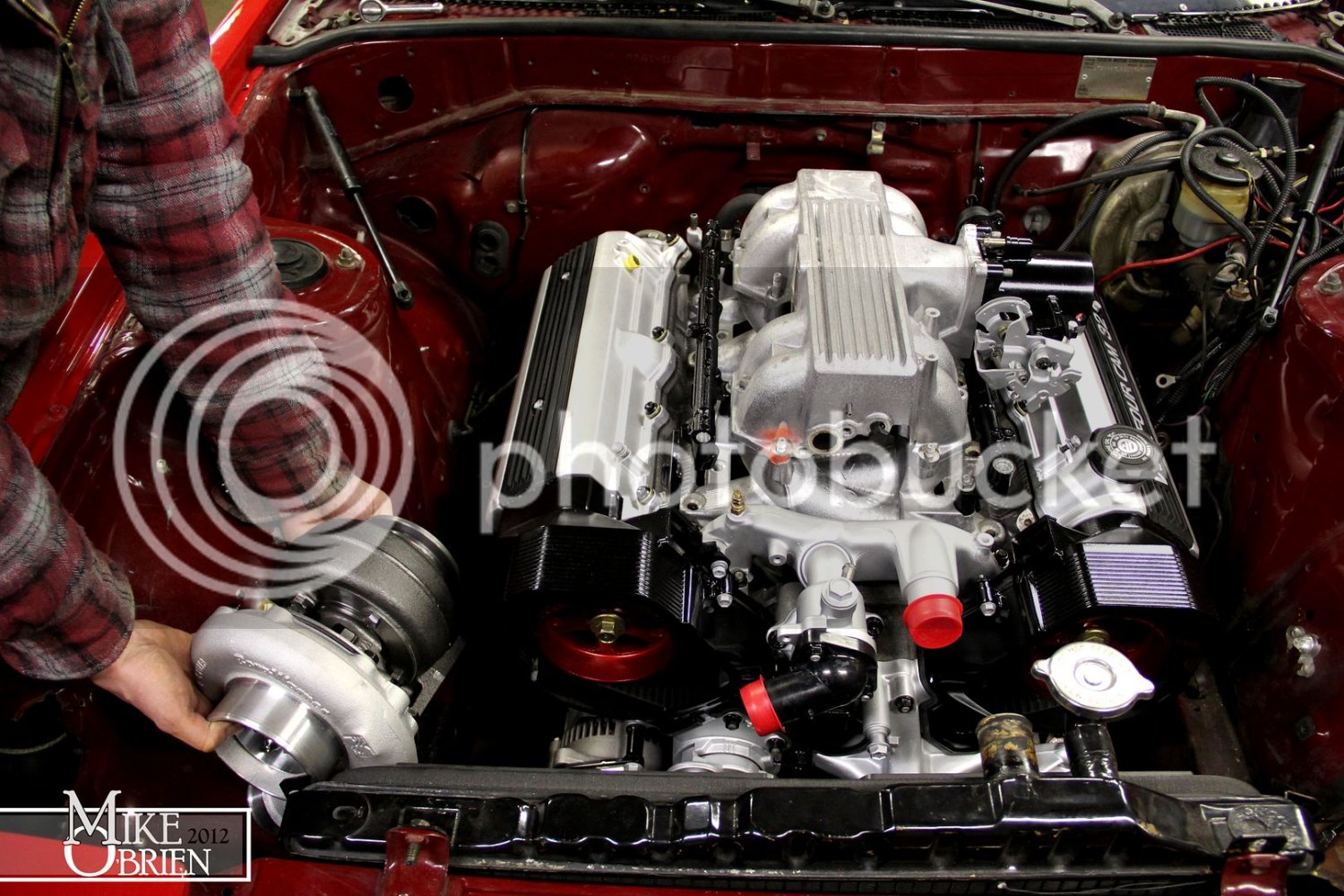
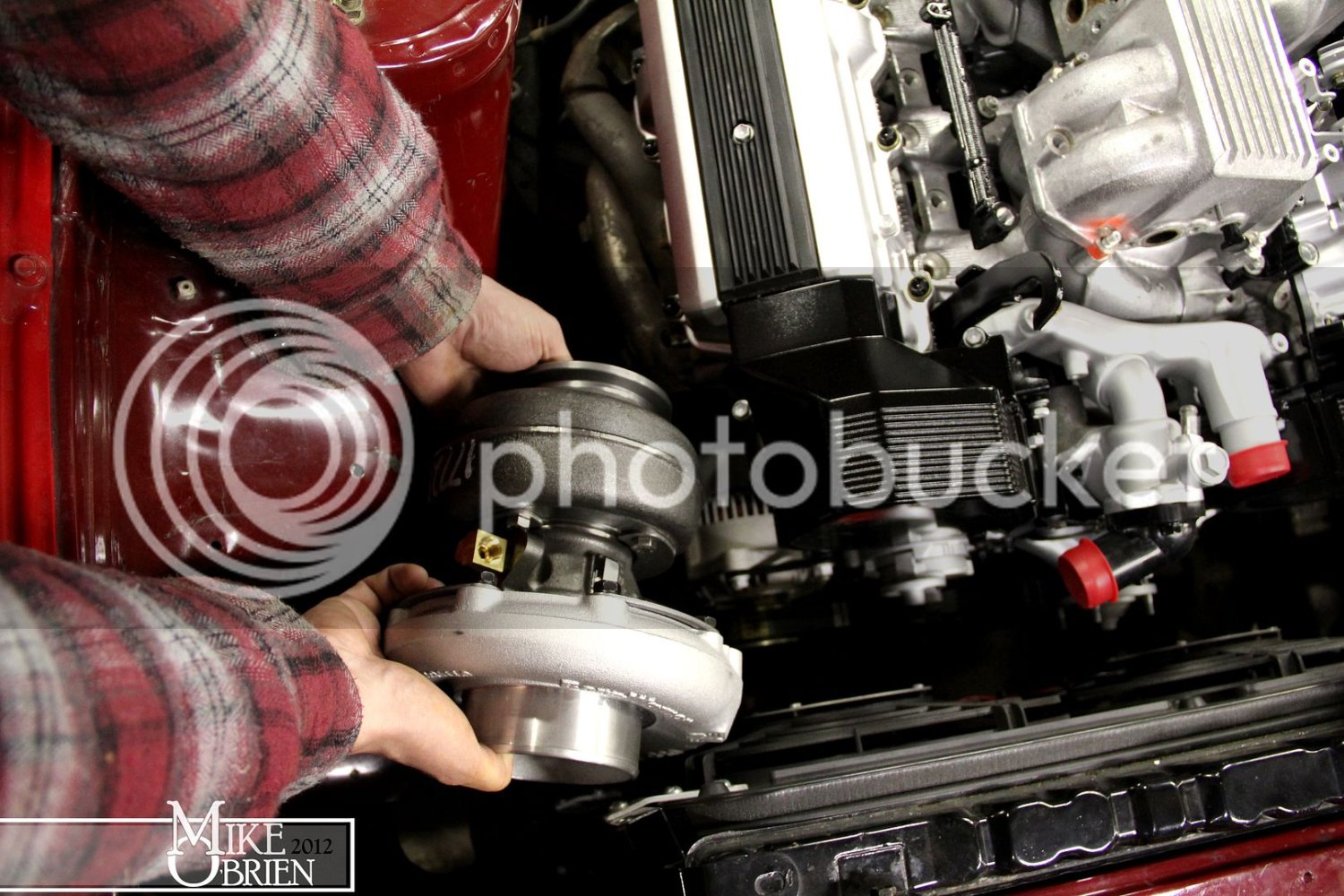
The hood closed with no issues with the manifold flipped around. I foresee no issues with clearance when the intercooler pipes are fabricated and mounted.
I am now thinking about what to do for a radiator. The driver's manifold needs a pipe to route to the passenger merge location, and I am worried about the lower rad hose outlet interfering with accessible routing. Also, I am worried about thicker aluminum radiators pushing the fans out even further and choking space up front.
I thought about mounting a radiator underneath the rad panel, but decided that was not the way to go since no viable options are there for inlets/outlets in an appropriate size. (Would need a 24”x14” radiator with suitable inlet/outlet) As of now, the Griffin 25241 looks like what I will go with. It is only 15.5 inches tall, which will allow it to sit a bit further in compared to the stock MKII radiator. Also, the cross flow inlet/outlets will better position the lower inlet to escape the driver's exhaust section.
http://www.summitracing.com/parts/GRI-1-25241-X/
I did alot of measuring and calculations, and I think I can actually fit the radiator (with a tiny bit of trimming on the rad panel) so that the fans will give a bit more clearance than what is currently available with the stock radiator.
More to come soon. Parts are coming in a steady flow, so lots of more projects should start springing up in the near future.
Thanks, -Mike