Oil pan came out pretty good. I'm happy with it. Does have one thin spot and one cold shunt. Both very small (smaller than a dime) and will be easy to touch up with TIG. The casting came out rough (surface finish), but I expected that as I poured hot since I was worried about it being such a large/thin part. I planned on smoothing the inside anyway, and will probably do the same on the outside.
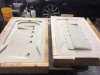
Two part resin/sand mold. Weighs over 200lbs.
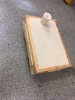
Ready to pour (no I did not pour it in my garage)
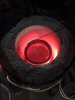
Melt ready to go (wire is the thermocouple for monitoring temperature)
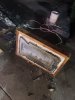
Mold opened. Notice how much the sand was burnt. This is a combination of pouring hot and having probably a bit too much resin in the sand. In any case, this results in a rougher surface finish on the casting.
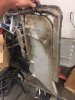
Outside (bottom). With runners/sprue/vents still attached.
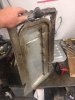
Inside. Pattern in the background.
Size came out perfect. Aluminum shrinks, so the pattern has to be sized appropriately. Can't say I have enough experience, but others are a wealth of knowledge - I just leaned on theirs and all came out good.
This pan allows for 5 evac lines (passenger side) and 1 turbo drain back line (drivers side). Just clears the rod bolts. I'll machine the pan for AN10 ORB fittings.