84pickup1uz
Fun Factor Garage - Canada Eh!
Just getting started on the physical work on this project. I've been doing research for several months and have acumulated a small mountain of cardboard boxes (parts) in the corner of my shop.
This truck project itself was started 10 years ago and at the time I had only access to a domestic engine (ford mustang 5.0). I will do a video on some of the 10-year-old work at some point later. I've recently sold off the highly tuned ford motor and purchased a 1UZ V8 from a 94 SC400.
The project was abruptly interrupted due to health complications with my firstborn son (who is fine now by the way). It was further delayed by several years while I helped build another vehicle for a younger family member. He has since passed away. Family always comes first in my life so this project has sat until recently.
When I retrieved the truck from storage I found a raccoon's nest in the cab complete with a large pile of dung! That was nasty! I could have filmed my own version of "ROADKILL" !! I ended up gutting most of the interior and the entire wiring harness. I've since bought a second 86 pickup for the parts I need to finish this one.
I am not a big fan of typing so I will be posting videos here fairly regularly. Here is my first video
The engine - first gen non vvt out of a 94 SC400
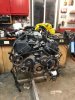
The Transmission is an R150F with down under bell housing and gear-driven transfer with 4.8:1 gears, dual shifter and upgraded from the output shaft. This came out of a serious rock crawler! I have a second transmission with fewer hard miles on it. Using this one for mock-up and to acquire all the adapter parts needed in one purchase.
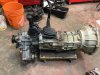
This is the ECU I just finished building Megasquirt version 3X
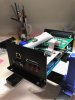
And this is an option! Note the spare intake manifold in the background. Planning to fab my own manifold. That should make for some entertainment.
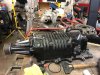
The mess from the Racoon! They made the front footwell into the latrine. I had already removed the large pile of dung at this point. The nest was behind the seats. It was nasty! the truck was stored inside but had no windows and the interior was mostly removed and in the box. They chewed on everything and crapped everywhere!
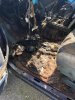
Here is a few pictures from 10 years ago just to set the stage.
This truck project itself was started 10 years ago and at the time I had only access to a domestic engine (ford mustang 5.0). I will do a video on some of the 10-year-old work at some point later. I've recently sold off the highly tuned ford motor and purchased a 1UZ V8 from a 94 SC400.
The project was abruptly interrupted due to health complications with my firstborn son (who is fine now by the way). It was further delayed by several years while I helped build another vehicle for a younger family member. He has since passed away. Family always comes first in my life so this project has sat until recently.
When I retrieved the truck from storage I found a raccoon's nest in the cab complete with a large pile of dung! That was nasty! I could have filmed my own version of "ROADKILL" !! I ended up gutting most of the interior and the entire wiring harness. I've since bought a second 86 pickup for the parts I need to finish this one.
I am not a big fan of typing so I will be posting videos here fairly regularly. Here is my first video
The engine - first gen non vvt out of a 94 SC400
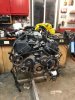
The Transmission is an R150F with down under bell housing and gear-driven transfer with 4.8:1 gears, dual shifter and upgraded from the output shaft. This came out of a serious rock crawler! I have a second transmission with fewer hard miles on it. Using this one for mock-up and to acquire all the adapter parts needed in one purchase.
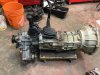
This is the ECU I just finished building Megasquirt version 3X
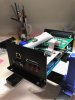
And this is an option! Note the spare intake manifold in the background. Planning to fab my own manifold. That should make for some entertainment.
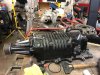
The mess from the Racoon! They made the front footwell into the latrine. I had already removed the large pile of dung at this point. The nest was behind the seats. It was nasty! the truck was stored inside but had no windows and the interior was mostly removed and in the box. They chewed on everything and crapped everywhere!
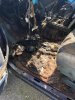
Here is a few pictures from 10 years ago just to set the stage.
Attachments
Last edited: