Justen, if you want to use the dual port actuator in a boost control scenario, as well as the classic recycle scenario, you're right, solenoid control is necessary.
The top port (above the diaphragm) pulls against the diaphragm and spring, and the actuator retracts and opens the recycle valve only under vac conditions.
The bottom port (under the diaphragm) pushes against the diaphragm and spring, the actuator retracts, and opens the recycle valve only under boost.
Obviously you have to do some isolation so you don't have the ports connected to the same signal at the same time. If you have equal pressure on each side of the diaphragm, nothing will happen.
The AEM boost control solenoid is a classic, normally closed, 3 way solenoid valve, where under deenergised conditions, the inlet port is blocked, and the outlet port is connected to the vent port. When it becomes energised, the inlet is now connected to the outlet, and the vent port is blocked.
Quite awhile ago, when I started looking for dual port actuators, I looked at 3 different control strategies under 4 different operating conditions and chose the strategy in the diagram below, however I have not tested it yet. It's only partially failsafe, in that it allows for a failure of SV2, however if SV1 fails, then under boost, the bypass valve will stay closed, which will allow maximum boost. So there still needs to be some safeguards, like rev & overboost limiters in the ECU that cut fuel & ignition.
Hopefully we'll get this tested on the next dyno session. Until then, if anyone wants to give it a go, be my guest. And if someone can come up with a better strategy, let's see it:
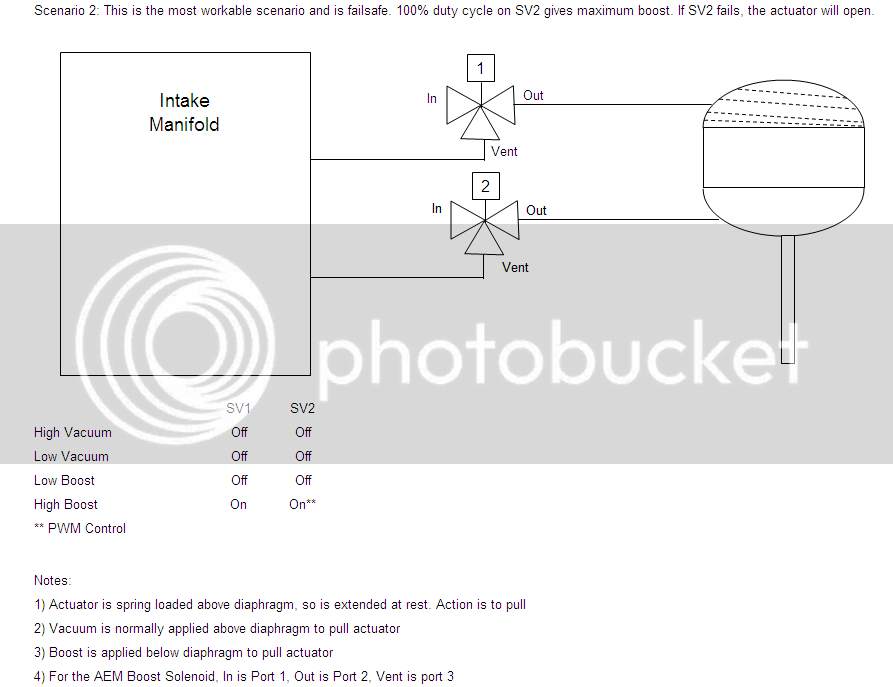