scotturnot
Member
- Messages
- 954
- Location
- central US
OK, so here is the dilemma. I have the awesome 14” Stoptech Brake set up and it won’t clear my rear wheels. I am really not at all interested in buying a new set of wheels with smaller lips and I can’t stand stretched tires with spacers. Pulling the fenders really is not for me either so what to do. Well I decided if I cant bring the wheels out I really have no choice but to push the brakes back in.
The following is a DIY to move the rear brakes inboard a half inch to allow low disc wheels to fit and retain that big fat lip. This is not a simple deal by any means but I never seem to follow the easy path.
First we have to move the calipers, the only way I see to do this is to physically cut off the caliper mounting ears and weld new ones on further back. The ears are .480” thick so they can be used to fixture the new ears to make sure they get in the exact location needed.
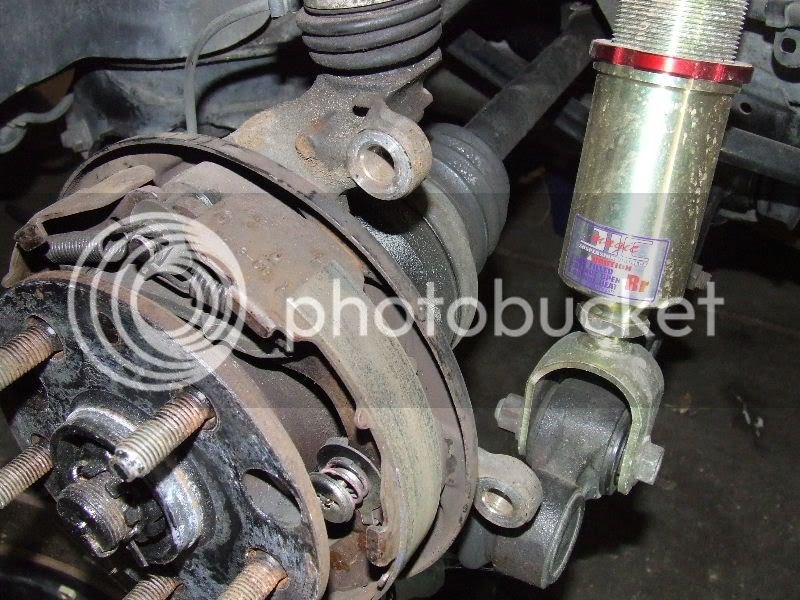
I started by making a set of new ears to replace the ones I will cut off.
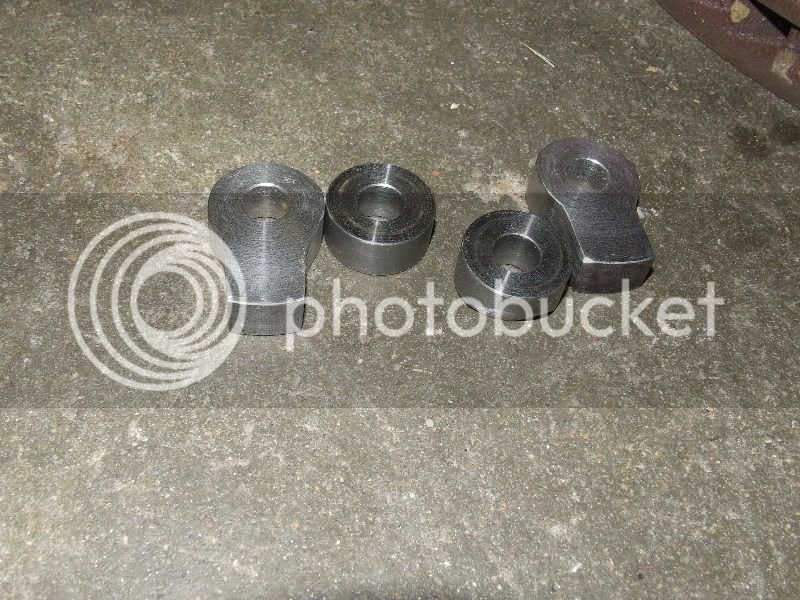
Next I bolted them to the backside of the stock ears to hold them in perfect location, this will set them back .480” from the original position, .020” shy of ½” close enough.
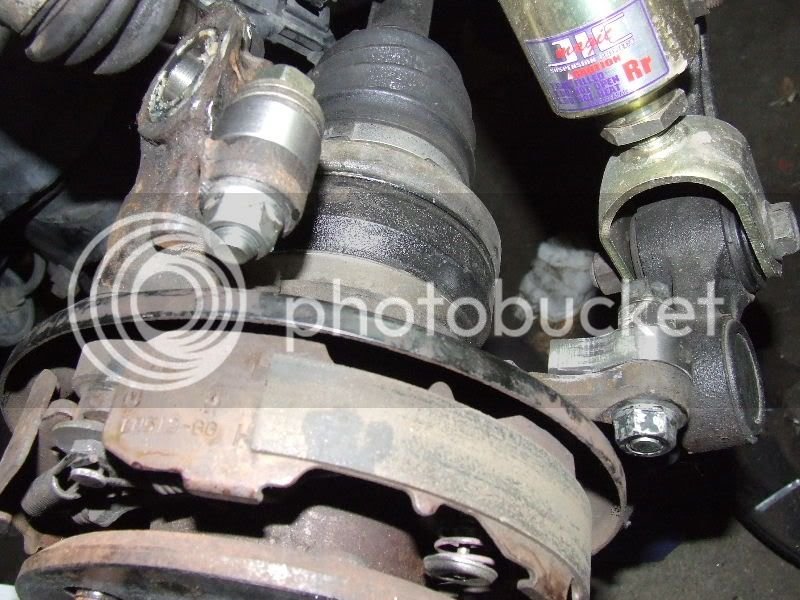
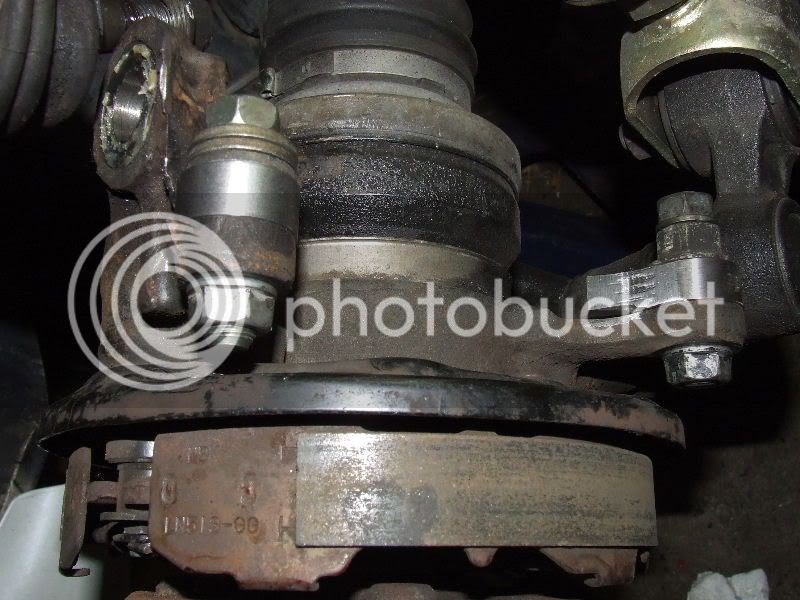
Next they get welded in place, I vee’ed out areas to be welded to allow for better penetration. Carful, don’t weld it to the front ear.
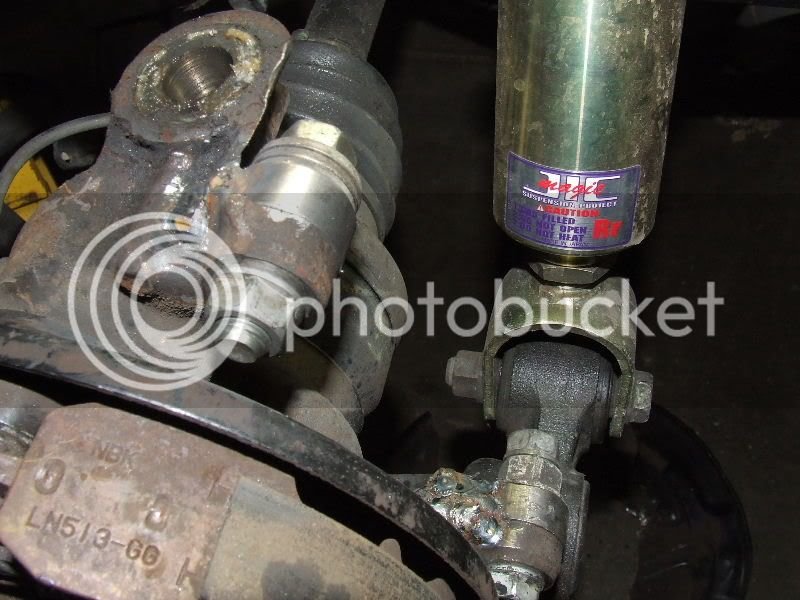
The following is a DIY to move the rear brakes inboard a half inch to allow low disc wheels to fit and retain that big fat lip. This is not a simple deal by any means but I never seem to follow the easy path.
First we have to move the calipers, the only way I see to do this is to physically cut off the caliper mounting ears and weld new ones on further back. The ears are .480” thick so they can be used to fixture the new ears to make sure they get in the exact location needed.
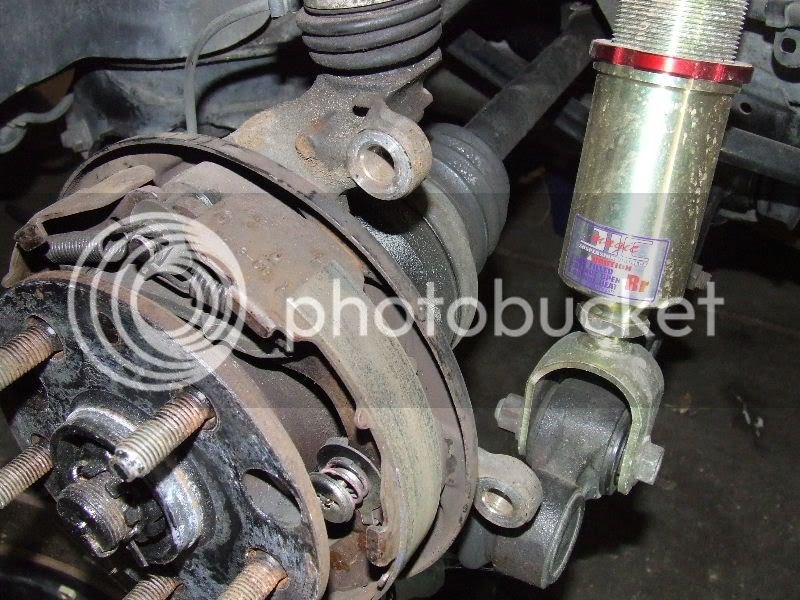
I started by making a set of new ears to replace the ones I will cut off.
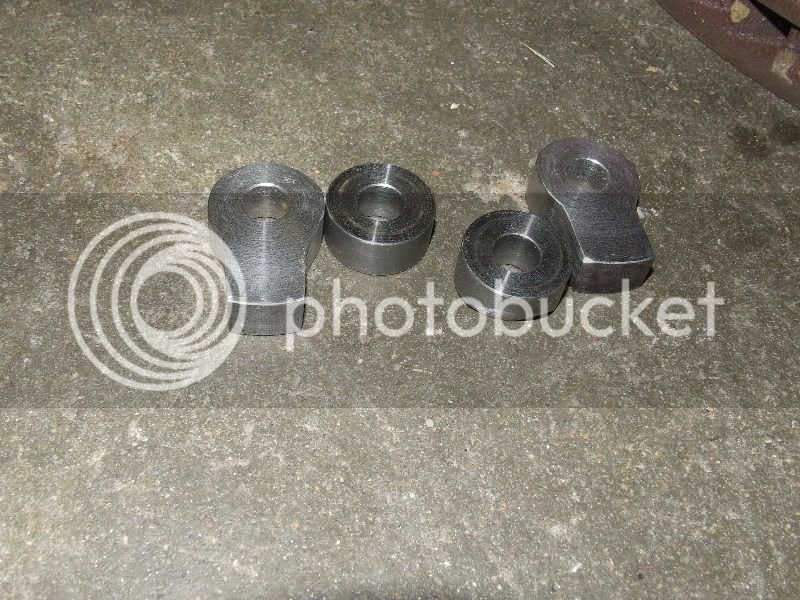
Next I bolted them to the backside of the stock ears to hold them in perfect location, this will set them back .480” from the original position, .020” shy of ½” close enough.
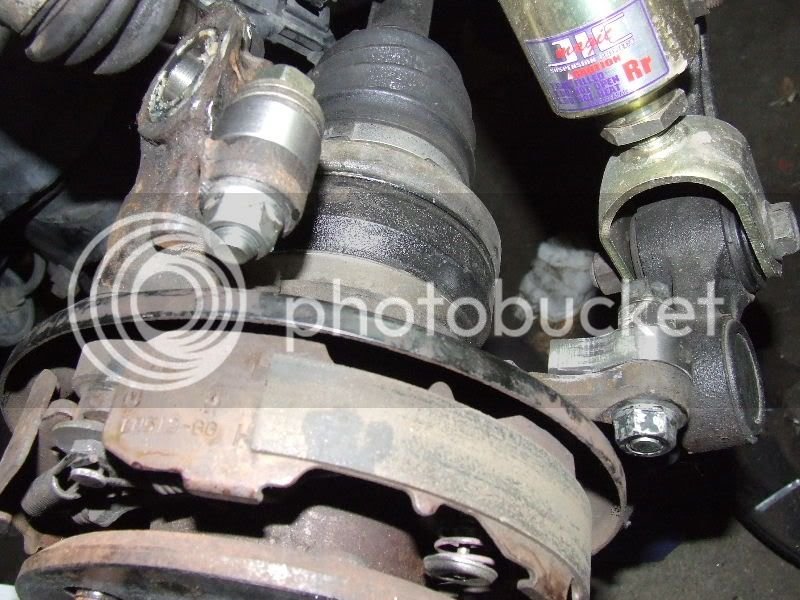
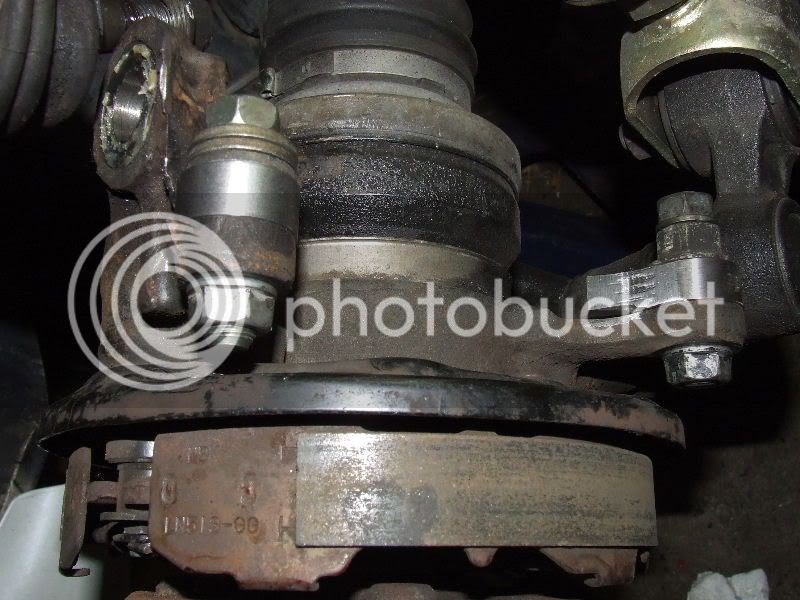
Next they get welded in place, I vee’ed out areas to be welded to allow for better penetration. Carful, don’t weld it to the front ear.
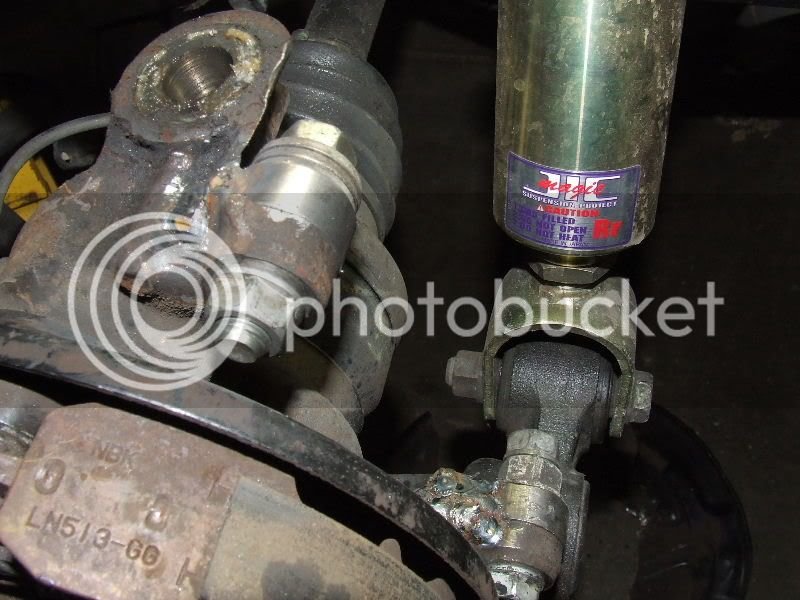