Something I've found recently that should be shared...
When setting up aftermarket ECU, there are often pre-configured tables you can use to align your coolant temp sensor reading with the actual temperature - effectively teaching the ECU how to read the sensor. In the case of a Haltech, you only get the choice of pre-configured tables for Toyota 1FZ-FE Coolant Sensor or Toyota JZX100 Coolant Sensor. You would think that, being Toyota as well, a 1UZ-FE Coolant sensor would be within range of one of these, but the readings I got were very wrong. Both of them had the dash reading 115 degrees with the fan running constantly. A pyrometer confirmed the sensor was much cooler.
Solution: I found a few charts in Toyota workshop manuals that gave the resistance range for the coolant temp sensor at -20, 0, 20, 40, 60, 80 and 100 degrees. After examining it carefully, I was able to map out the upper and lower resistances for each temperature range - and from that, determine the averages. With these average numbers programmed into the sensor calibration, it reads properly now and this is confirmed with the pyrometer.
I also wanted it to measure temperature up to a theoretical 120 degrees in 10 degree increments, so with a bit of simple maths, I filled the gaps in between. Here are the results (in KiloOhms).
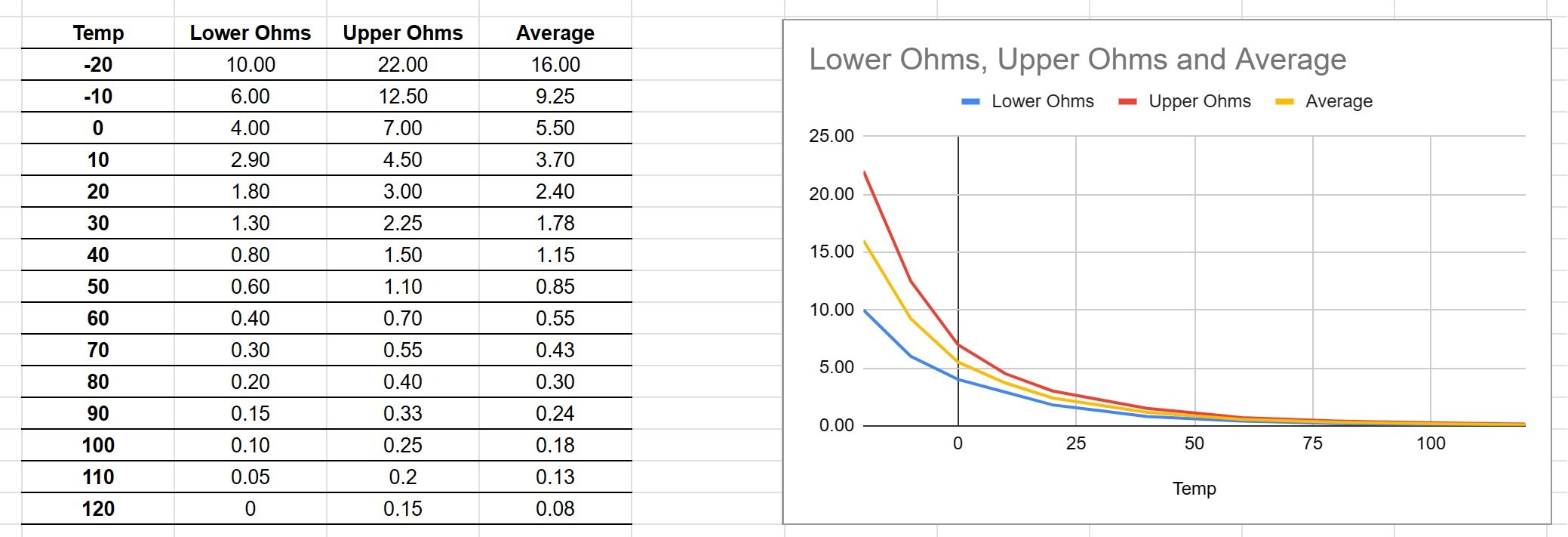
I would be interested to know what others have used in their setup and how accurate the readings are.
Cheers,
PB
When setting up aftermarket ECU, there are often pre-configured tables you can use to align your coolant temp sensor reading with the actual temperature - effectively teaching the ECU how to read the sensor. In the case of a Haltech, you only get the choice of pre-configured tables for Toyota 1FZ-FE Coolant Sensor or Toyota JZX100 Coolant Sensor. You would think that, being Toyota as well, a 1UZ-FE Coolant sensor would be within range of one of these, but the readings I got were very wrong. Both of them had the dash reading 115 degrees with the fan running constantly. A pyrometer confirmed the sensor was much cooler.
Solution: I found a few charts in Toyota workshop manuals that gave the resistance range for the coolant temp sensor at -20, 0, 20, 40, 60, 80 and 100 degrees. After examining it carefully, I was able to map out the upper and lower resistances for each temperature range - and from that, determine the averages. With these average numbers programmed into the sensor calibration, it reads properly now and this is confirmed with the pyrometer.
I also wanted it to measure temperature up to a theoretical 120 degrees in 10 degree increments, so with a bit of simple maths, I filled the gaps in between. Here are the results (in KiloOhms).
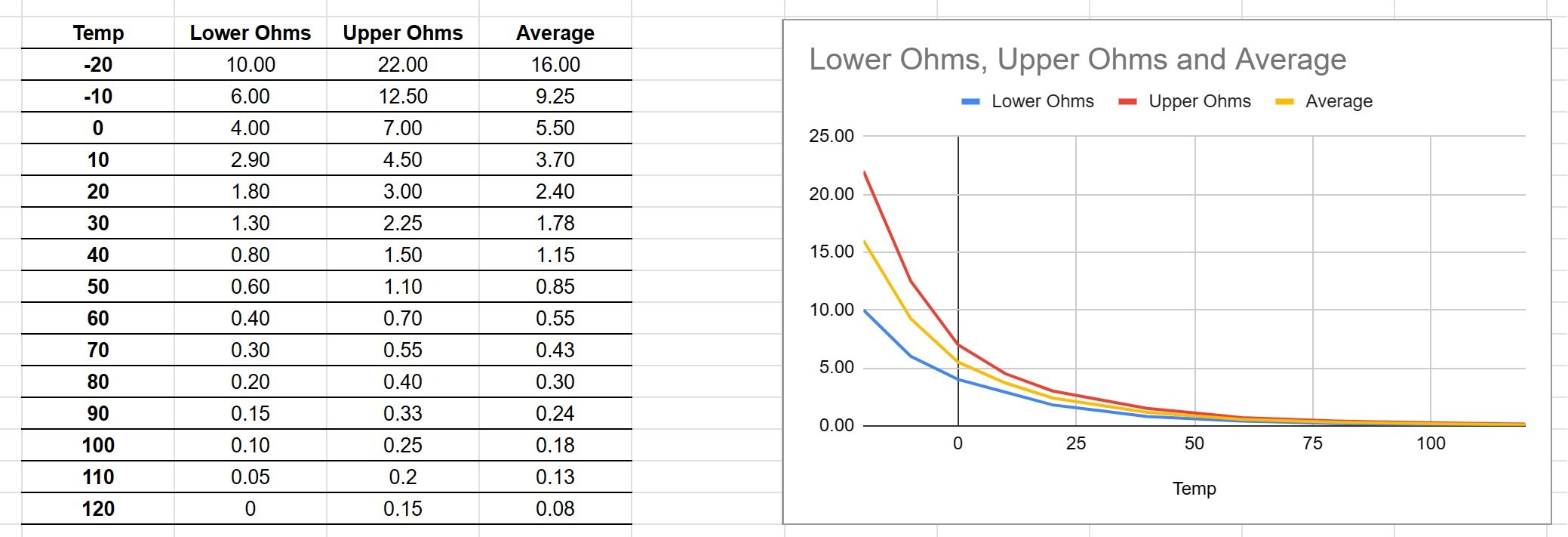
I would be interested to know what others have used in their setup and how accurate the readings are.
Cheers,
PB