striker
New Member
Hey all,
been a while I guess but with an excuse this time.
been practicing on my AC tig skills for a good week! yes I bought one finally, probably not a known make to non euro people.
It´s a Gys 207 Tig welder. 10 to 200A, 20 to 200hz ac, pulse, fully digital. I got a very good price because this was a demo model, but never used, since I bought it before they could open the box.....:beerchug:
After running lots of pratice beads on 1 and 2 mm sheet alloy I took the plunge and went out shopping for 9 meters of 15mm square tube aluminium, and some 3mm x 35mm strip.
remember the Mig Rig on the wooden 6 wheel dolly, well that doesn´t exist anymore exept for the dolly now carrying the transaxle gearbox.
I made an all new trolley to carry both the Mig and the Tig machines. Not every weld came out looking nice, (strange thing that is, one weld is looking very nice the next looks rubbish... how come) tig welding is very hard to do well.
anyway it still hasn´t collapsed under the weight of both welders and the larger bottle of argon.....
piccies
the old mig rig
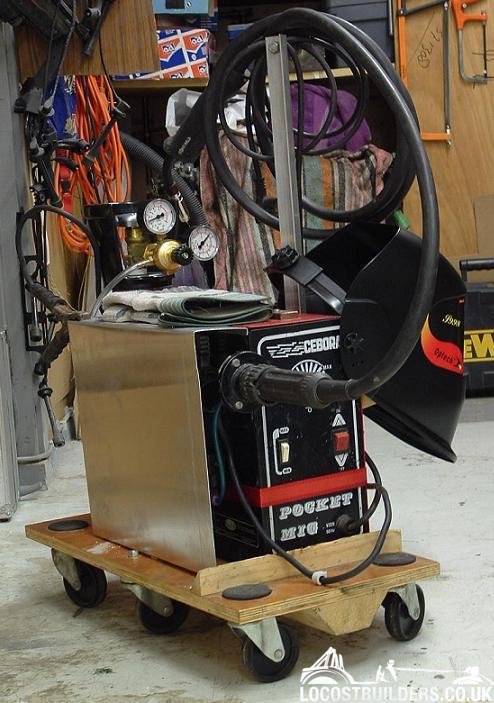
New ally wheels
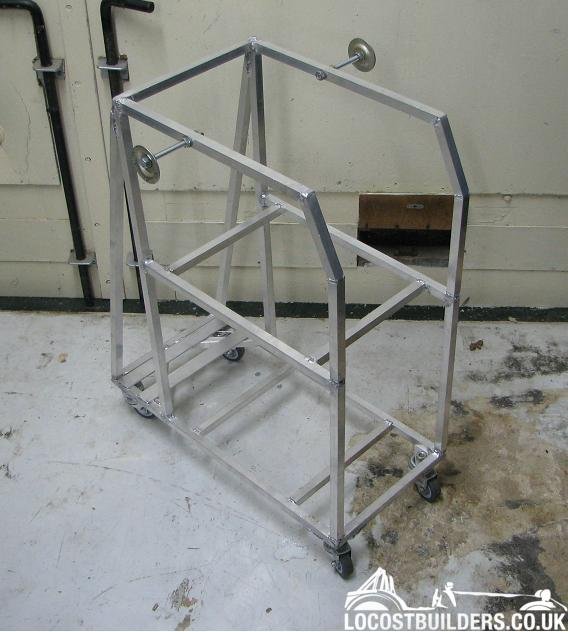
and fully equiped
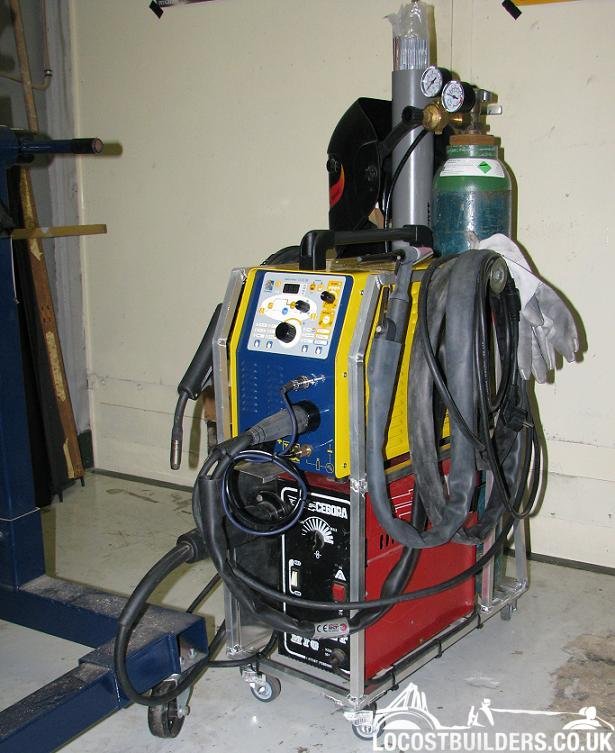
now lets build some intercoolers,
grtz Thomas
been a while I guess but with an excuse this time.
been practicing on my AC tig skills for a good week! yes I bought one finally, probably not a known make to non euro people.
It´s a Gys 207 Tig welder. 10 to 200A, 20 to 200hz ac, pulse, fully digital. I got a very good price because this was a demo model, but never used, since I bought it before they could open the box.....:beerchug:
After running lots of pratice beads on 1 and 2 mm sheet alloy I took the plunge and went out shopping for 9 meters of 15mm square tube aluminium, and some 3mm x 35mm strip.
remember the Mig Rig on the wooden 6 wheel dolly, well that doesn´t exist anymore exept for the dolly now carrying the transaxle gearbox.
I made an all new trolley to carry both the Mig and the Tig machines. Not every weld came out looking nice, (strange thing that is, one weld is looking very nice the next looks rubbish... how come) tig welding is very hard to do well.
anyway it still hasn´t collapsed under the weight of both welders and the larger bottle of argon.....
piccies
the old mig rig
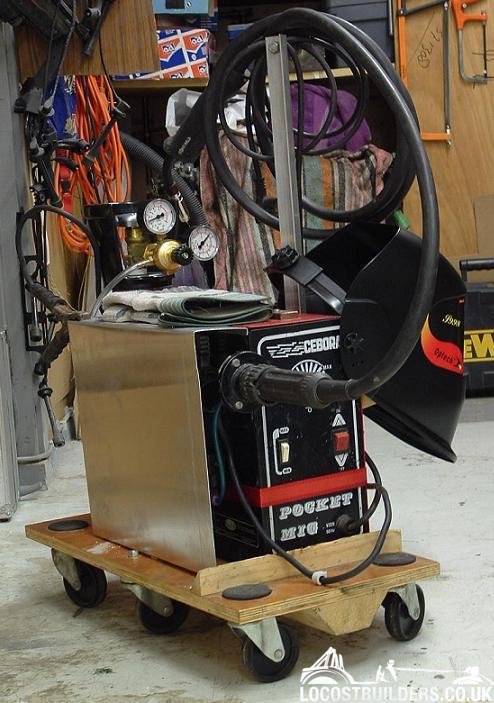
New ally wheels
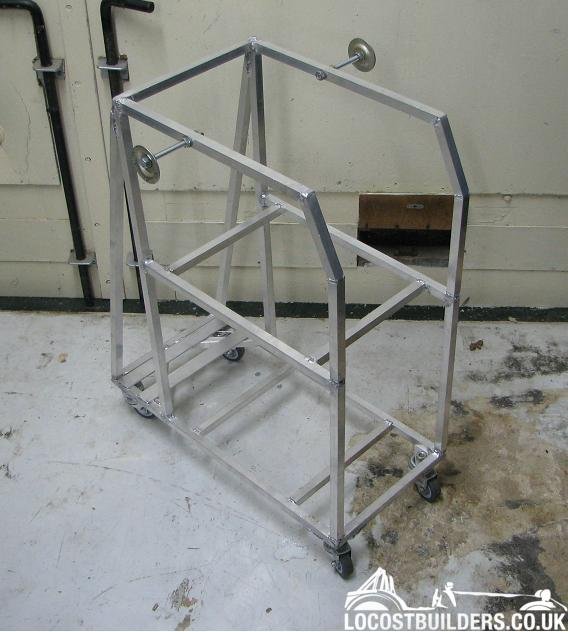
and fully equiped
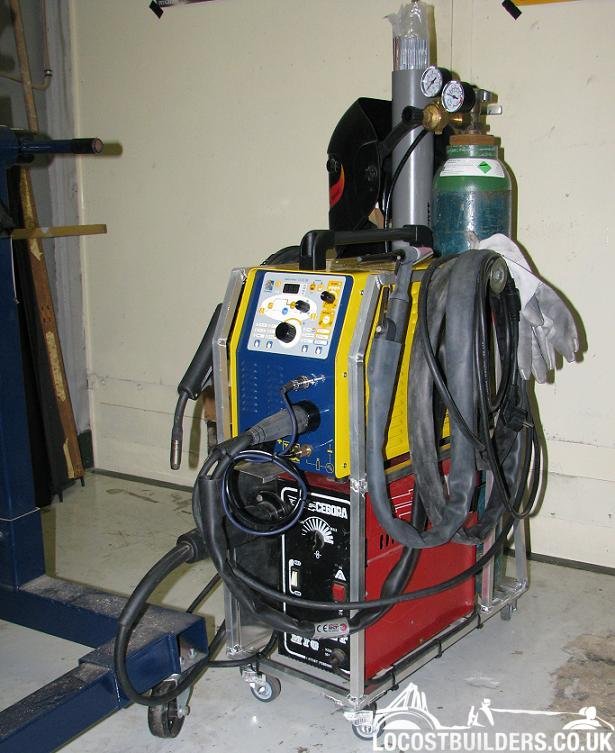
now lets build some intercoolers,
grtz Thomas