striker
New Member
Hey all,
Yesterday was treat myself day, because the summer has been lousy and I just needed to spend some money which would have normaly gone down the fillercap on the striker.
so I bought an older cebora Mig machine 125apms which had been converted to run gas. it was in pretty bad shape but a day of fidling with the wire feeder and the gasvalve + making a new side cover because the old one wasn't there, I was finaly ready to do my first practice this evening.
I have very little experience in welding myself, so I did a few tests on 3 pieces of round 4301 steel tube 1.5mm wallthickness I had lying around. tell me what you think. if it's ok I can finally start on the SC mounts for the engine.
here's the machine
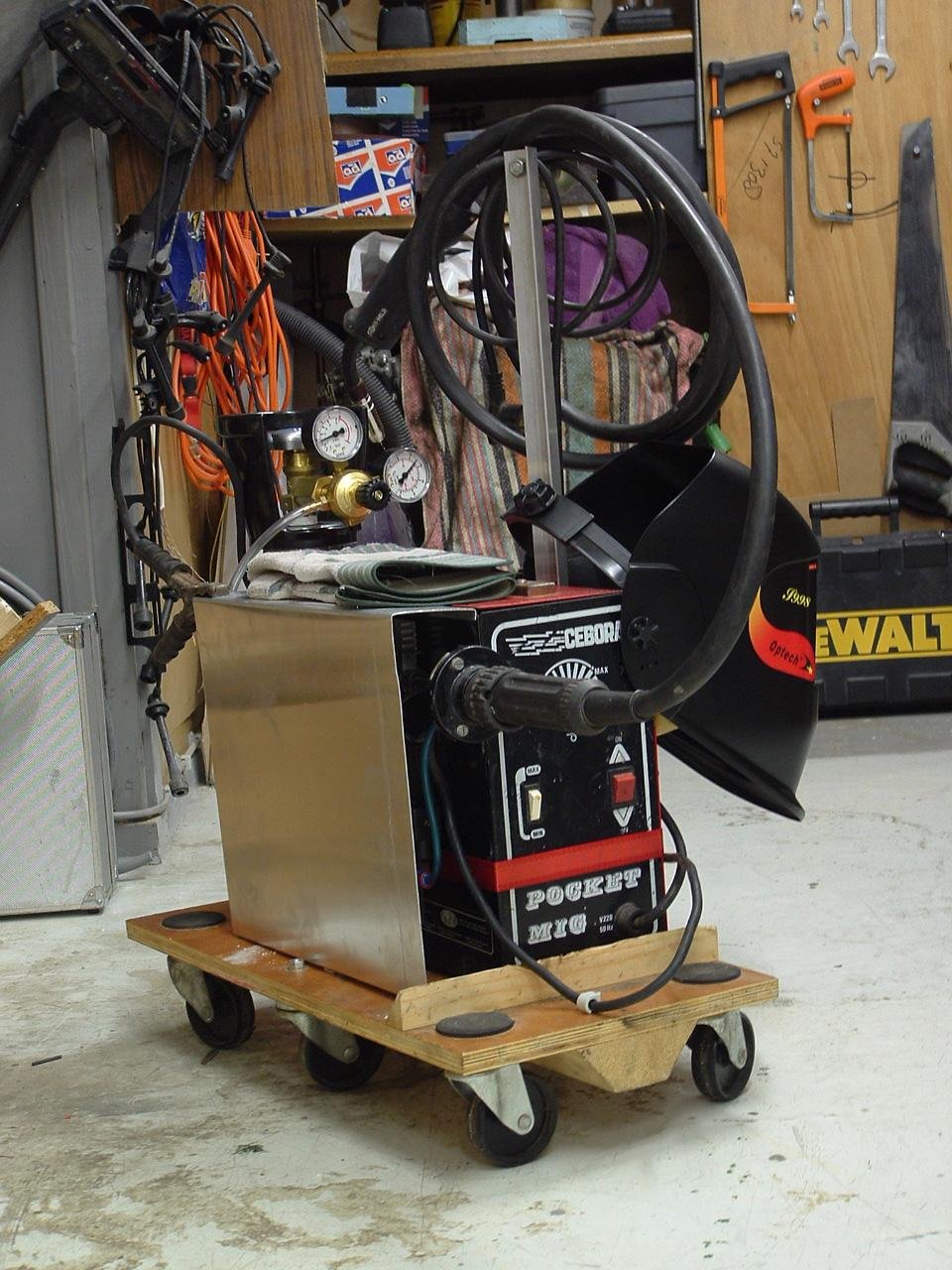
here's the welds
the left one is the first try and the right one is the second with a little more wire feed which made it sound the way I normally hear my friend doing it, a sort of "crispy" is that right? I cleaned the right one with a wire brush
I had the current on low mode, but I don't realy understand the gas meter, I turned it up some and the welds don't look poreus so it's probably ok, can you have to much gas?

Grtz Thomas
Yesterday was treat myself day, because the summer has been lousy and I just needed to spend some money which would have normaly gone down the fillercap on the striker.
so I bought an older cebora Mig machine 125apms which had been converted to run gas. it was in pretty bad shape but a day of fidling with the wire feeder and the gasvalve + making a new side cover because the old one wasn't there, I was finaly ready to do my first practice this evening.
I have very little experience in welding myself, so I did a few tests on 3 pieces of round 4301 steel tube 1.5mm wallthickness I had lying around. tell me what you think. if it's ok I can finally start on the SC mounts for the engine.
here's the machine
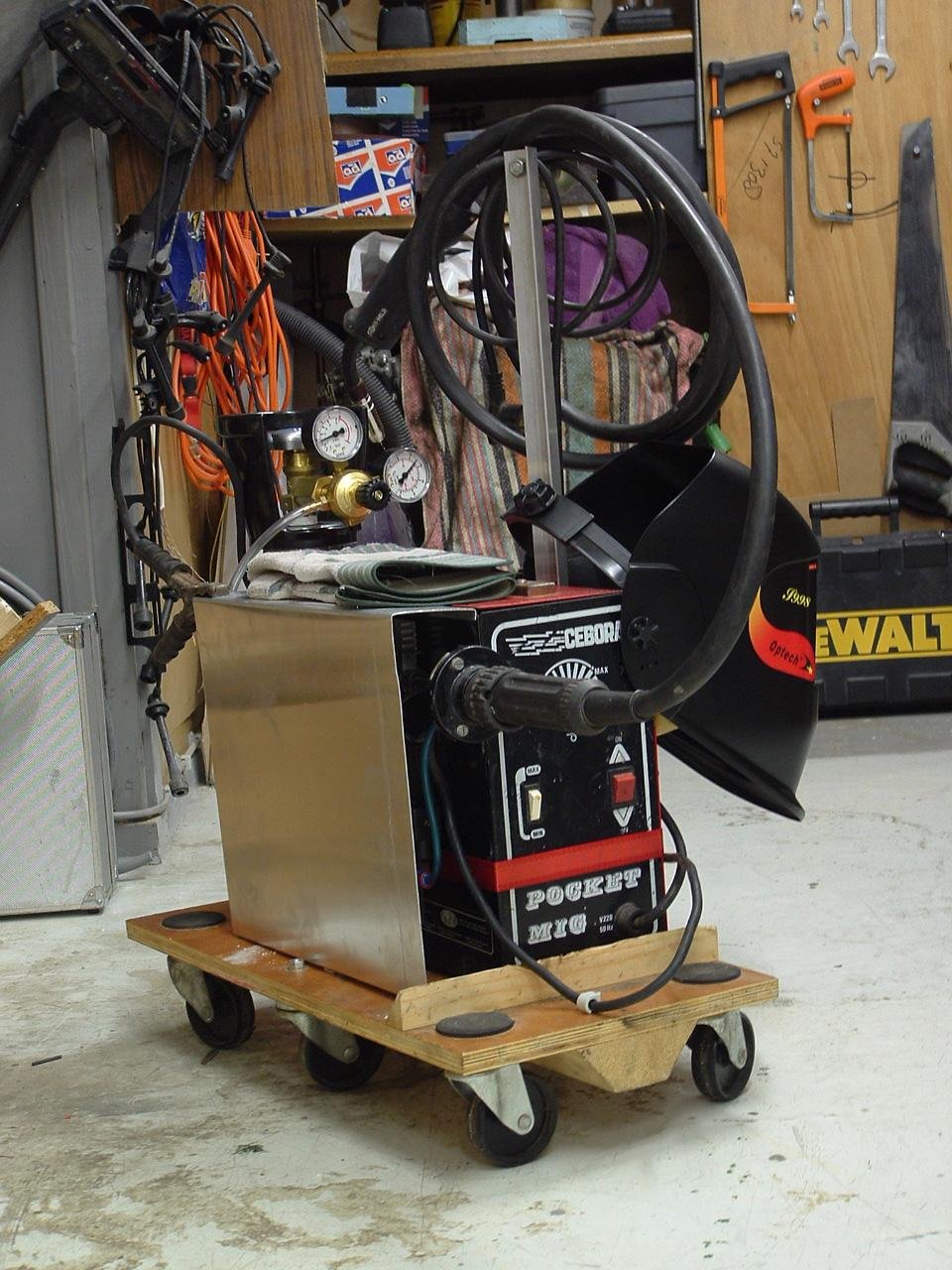
here's the welds
the left one is the first try and the right one is the second with a little more wire feed which made it sound the way I normally hear my friend doing it, a sort of "crispy" is that right? I cleaned the right one with a wire brush
I had the current on low mode, but I don't realy understand the gas meter, I turned it up some and the welds don't look poreus so it's probably ok, can you have to much gas?

Grtz Thomas